Heat treatment technology of aviation aluminum alloy
With the development of transportation technology, aluminum alloy has been widely used in aviation materials due to its light weight, high strength, and convenient processing. The effective application of aluminum alloy reduces the structural weight of aircraft, improves flight performance and increases economic benefits. Therefore, aviation aluminum alloy technology has also received more attention.
Heat treatment of aluminum alloy with air circulation electric furnace instead of nitrate furnace
Traditional heat treatment uses a nitrate furnace for heating, which has the disadvantages of serious environmental pollution, energy consumption and waste, while the air circulation electric furnace has the advantages of fast start-up and good energy-saving effect, and the quenching transfer time is fast and adjustable, which can meet the requirements of different aluminum alloy parts. Require. After the air circulation electric furnace is heated, solution quenching does not pollute the cooling medium, which is beneficial to popularize the use of organic quenching medium, reduce heat treatment distortion, and improve production efficiency.
The key technology of the air circulation electric furnace is how to ensure the uniformity of furnace temperature (±3~±5℃), especially for large-sized furnaces, and how to meet the requirements of lower temperature (100~150℃) furnace temperature uniformity. The second key technology is how to ensure rapid quenching transfer time, and can be adjusted and controlled according to different requirements of parts.
Organic quenching medium
Aluminum alloy quenching medium is commonly used water or hot water, but for the heat treatment deformation is large or the deformation is strict, the hot water cannot meet the requirements, and the organic quenching medium aqueous solution must be selected. The use of organic quenching medium aqueous solution instead of water on the air circulation electric furnace reduces the heat treatment deformation of aluminum alloy and the correction time of sheet metal parts by more than 50%.
Conductivity detection
Since aluminum alloy materials are used in aircraft manufacturing, tensile tests or hardness tests have been used to detect the quality of aluminum alloy heat treatment. After the aluminum alloy is heat-treated, under one strength (hardness) value, there may be two different states, and vice versa, under one state, there may be two different strength (hardness) values. Therefore, only using hardness or strength to control the quality of aluminum alloy after heat treatment is an outdated detection method and cannot completely ensure the quality.
Conductivity detection has the unique advantages of convenience and quickness, high work efficiency, and is basically not restricted by the shape and weight of the inspected part, and has the unique advantage of no damage to the part. Since the 1980s, conductivity detection has gradually been widely used in the heat treatment state inspection of aluminum alloy materials/parts in China. In the GB/T12966-1991 "Aluminum Alloy Electrical Conductivity Eddy Current Test Method" standard, the test method is given, GJB2894-l997 "Aluminum Alloy Electrical Conductivity and Hardness Requirements", which clarifies the electrical conductivity and hardness value requirements.
Link to this article: Heat treatment technology of aviation aluminum alloy
Reprint Statement: If there are no special instructions, all articles on this site are original. Please indicate the source for reprinting:https://www.cncmachiningptj.com
PTJ® is a customized manufacturer that provides a full range of copper bars, brass parts and copper parts. Common manufacturing processes include blanking, embossing, coppersmithing, wire edm services, etching, forming and bending, upsetting, hot forging and pressing, perforating and punching, thread rolling and knurling, shearing, multi spindle machining, extrusion and metal forging and stamping. Applications include bus bars, electrical conductors, coaxial cables, waveguides, transistor components, microwave tubes, blank mold tubes, and powder metallurgy extrusion tanks.
Tell us a little about your project’s budget and expected delivery time. We will strategize with you to provide the most cost-effective services to help you reach your target,You are welcome to contact us directly ( sales@pintejin.com ) .
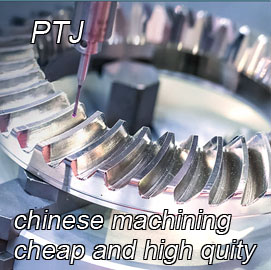
- 5 Axis Machining
- Cnc Milling
- Cnc Turning
- Machining Industries
- Machining Process
- Surface Treatment
- Metal Machining
- Plastic Machining
- Powder Metallurgy Mold
- Die Casting
- Parts Gallery
- Auto Metal Parts
- Machinery Parts
- LED Heatsink
- Building Parts
- Mobile Parts
- Medical Parts
- Electronic Parts
- Tailored Machining
- Bicycle Parts
- Aluminum Machining
- Titanium Machining
- Stainless Steel Machining
- Copper Machining
- Brass Machining
- Super Alloy Machining
- Peek Machining
- UHMW Machining
- Unilate Machining
- PA6 Machining
- PPS Machining
- Teflon Machining
- Inconel Machining
- Tool Steel Machining
- More Material