Why is the difficulty of SS machining so high?
Analyze The Difficulty Of SS Cnc Machining
There are many types of stainless steel like 304, 303, but most of machinist have the same feeling that non-standard stainless steel is difficult to machining. |
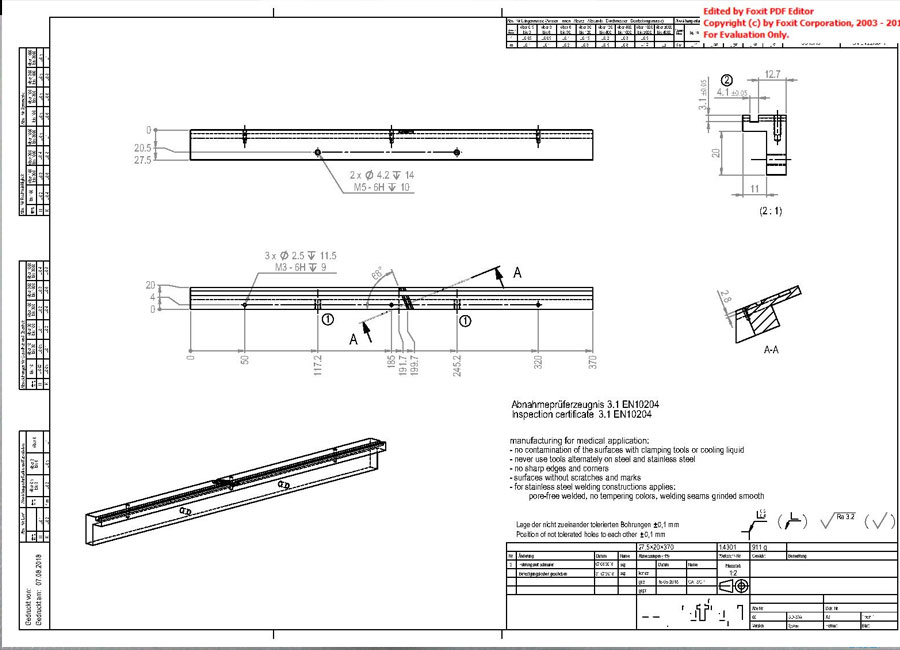
In fact, the reasons for the difficulty in processing are the following:
1: The chemical relationship between the tool and the material to be processed causes work hardening and low thermal conductivity of the material to be processed. Not only is it easy to cause unusual wear and tear, but also the tool is chipped and abnormally broken.
2: Low thermal conductivity causes plastic deformation of the cutting pin and faster tool wear.
3: The built-up edge is easy to cause small pieces of debris to remain on the cutting edge and cause poor processing of the surface.
4: The hardness of the machining causes the tool to wear faster and it is difficult to chip.
Existing solutions to the above problems, PTJ Shop recommended solutions are as follows:
1.tool material selection
Due to the high cutting force and high cutting temperature when processing stainless steel parts, it is possible to use a cubic hydrogenated turning blade that is second only to diamond and can withstand very high temperatures. In addition, its chemical inertness is very large, and it does not play a chemical role with the iron group metal at 1200~1300 °C, so it is very suitable for processing stainless steel materials.
2. tool geometry parameters
The geometrical parameters of the tool play an important role in the cutting performance. In order to make the cutting light and smooth, the carbide tool should adopt a larger front angle to improve the tool life. This is conducive to strengthening the blade and giving full play to the superiority of the ceramic tool with high compressive strength. The size of the back angle directly affects tool wear and has an effect on the strength of the blade. The change in the lead angle affects the variation of the radial and component cutting forces as well as the cutting width and the thickness of the cutting.
3. The roughness value of the rake face should be small when sharpening
In order to avoid chip sticking, the front and back flank of the tool should be carefully sharpened to ensure a small roughness value, thus reducing chip outflow resistance and avoiding chip sticking.
4. the cutting edge of the tool should be sharp
The cutting edge of the tool should be sharp to reduce work hardening. The feed and backing amount should not be too small to prevent the cutting of the tool in the hardened layer and affect the service life of the tool.
5.pay attention to the grinding of the chipbreaker
Due to the toughness of the stainless steel chips, the chipbreaker on the tool rake face should be properly ground, which makes it easy to interrupt the chip, chip and chip.
6.the choice of cutting oil should be appropriate
Since stainless steel has the characteristics of easy adhesion and poor heat dissipation, it is very important to use cutting oil with good adhesion and heat dissipation in cutting, such as Yida 渤 Run which has good cooling, cleaning, rust and lubrication effects. Special stainless steel cutting oil.
7.the choice of cutting amount
According to the characteristics of stainless steel materials, it is advisable to use low speed and large feed for cutting. By adopting the above-mentioned process method, the processing difficulty of the stainless steel can be overcome, the tool life of the stainless steel is greatly improved during the cutting process, the number of times of the knife change in the operation is reduced, the production efficiency and the cutting precision are improved, and the labor intensity of the worker is reduced. In terms of comprehensive production costs, satisfactory results can be obtained.
Link to this article: Why is the difficulty of SS machining so high?
Reprint Statement: If there are no special instructions, all articles on this site are original. Please indicate the source for reprinting:https://www.cncmachiningptj.com/,thanks!
PTJ® provides a full range of Custom Precision cnc machining china services.ISO 9001:2015 &AS-9100 certified. 3, 4 and 5-axis rapid precision CNC machining services including milling, turning to customer specifications,Capable of metal & plastic machined parts with +/-0.005 mm tolerance.Secondary services include CNC and conventional grinding, drilling,die casting,sheet metal and stamping.Providing prototypes, full production runs, technical support and full inspection.Serves the automotive, aerospace, mold&fixture,led lighting,medical,bicycle, and consumer electronics industries. On-time delivery.Tell us a little about your project’s budget and expected delivery time. We will strategize with you to provide the most cost-effective services to help you reach your target,Welcome to Contact us ( sales@pintejin.com ) directly for your new project.
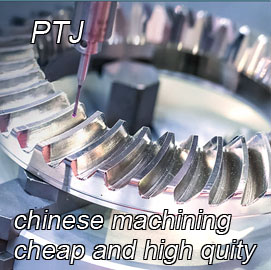
- 5 Axis Machining
- Cnc Milling
- Cnc Turning
- Machining Industries
- Machining Process
- Surface Treatment
- Metal Machining
- Plastic Machining
- Powder Metallurgy Mold
- Die Casting
- Parts Gallery
- Auto Metal Parts
- Machinery Parts
- LED Heatsink
- Building Parts
- Mobile Parts
- Medical Parts
- Electronic Parts
- Tailored Machining
- Bicycle Parts
- Aluminum Machining
- Titanium Machining
- Stainless Steel Machining
- Copper Machining
- Brass Machining
- Super Alloy Machining
- Peek Machining
- UHMW Machining
- Unilate Machining
- PA6 Machining
- PPS Machining
- Teflon Machining
- Inconel Machining
- Tool Steel Machining
- More Material