Production of lightweight parts based on thermoset plastics
Glass fiber reinforced plastic (FRP) is also called GFRP, that is fiber reinforced plastic, generally refers to the use of glass fiber reinforced unsaturated polyester, epoxy resin and phenolic resin matrix.
Reinforced plastics that use glass fiber or its products as reinforcing materials are called glass fiber reinforced plastics, or glass fiber reinforced plastics. High-hardness functional glass fiber reinforced plastic has great development prospects not only in the automobile manufacturing industry, but also in the aviation industry. Therefore, the German Institute of Industrial Plastics Processing (IKV) and the Technical Process Institute of RWTH Aachen University are concentrating on the research and development of thermosetting plastic-based and economical glass fiber reinforced plastic (FRP) processed by injection molding process (FRP).
Due to the high mechanical strength and low density of FRP (only 25% of metal) ②, the demand for FRP in industrial production is increasing day by day. Therefore, how to improve the economic efficiency of FRP production and shorten the production cycle time has always been the subject of various research projects. Since FRP based on thermoplastics has been mass-produced and widely used in industry, the German Industrial Plastics Processing Research Institute will produce FRP based on thermosetting plastics for the first time. Because thermosetting plastics have low temperature resistance, high mechanical strength, and good heat resistance, in many applications, the performance of thermosetting plastics is better than that of thermoplastics.
In the current research project, the research team of the German Industrial Plastics Processing Institute is studying the possibility of producing lightweight parts based on thermosetting plastics. Similar to the known integrated molding and re-injection process of FRP ③ based on thermoplastics, its research purpose is to combine good lightweight performance with the possible complexity of injection molding and apply it to thermoset plastic parts . The scientific research team adopted two process innovation routes: one is a two-step process route, involving the back molding technology of the established RTM④ process production parts; the other is a one-step process route, involving beam dipping/prepreg The back molding technology of the material, combined with this process, is cured in the injection molding process. Compared with traditional production processes (such as bonding and riveting), both process routes can simplify the production steps and shorten the production cycle.
As part of the Economic Affairs of the German Federal Government and the Energy Industry Research (IGF) of the Bundestag, the IGF 9EWN project is funded by AiF.
Note: ①Glass steel, scientific name fiber reinforced plastics, commonly known as FRP (Fiber Reinforced Plastics), namely fiber reinforced composite plastics, it uses glass fiber and its products (glass cloth, tape, felt, yarn, etc.) as reinforcing materials, and synthetic resin A composite material used as a matrix material.
②The relative density is between 1.5 and 2.0, which is only 20% to 25% of carbon steel, but the tensile strength is close to or even higher than that of carbon steel, and the specific strength can be compared with high-grade alloy steel.
③The German Industrial Plastics Processing Research Institute selected a football shin guard as an exhibit in 2014, showing the use of injection molding to process fiber-reinforced plastics based on thermoplastics. The project uses technologies such as in-situ polymerization to combine the advantages of the melt impregnation process (fabric preforms can be processed) with the advantages of the thermoplastic matrix.
④RTM (Resin Transfer Molding) is the abbreviation for resin transfer molding, and it is one of the main development directions of Cost Effective Manufacture Technology for advanced composite materials in aerospace. RTM molding technology is a new composite material molding technology evolved from the injection molding process and wet layup process. Since the 1980s, RTM technology has been widely used in foreign countries to produce automobile instrument panels, bumpers, and engine covers. , Car body and other auto parts.
Link to this article:Production of lightweight parts based on thermoset plastics
Reprint Statement: If there are no special instructions, all articles on this site are original. Please indicate the source for reprinting:https://www.cncmachiningptj.com
PTJ® is a customized manufacturer that provides a full range of copper bars, brass parts and copper parts. Common manufacturing processes include blanking, embossing, coppersmithing, wire edm services, etching, forming and bending, upsetting, hot forging and pressing, perforating and punching, thread rolling and knurling, shearing, multi spindle machining, extrusion and metal forging and stamping. Applications include bus bars, electrical conductors, coaxial cables, waveguides, transistor components, microwave tubes, blank mold tubes, and powder metallurgy extrusion tanks.
Tell us a little about your project’s budget and expected delivery time. We will strategize with you to provide the most cost-effective services to help you reach your target,You are welcome to contact us directly ( sales@pintejin.com ) .
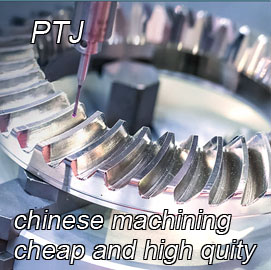
- 5 Axis Machining
- Cnc Milling
- Cnc Turning
- Machining Industries
- Machining Process
- Surface Treatment
- Metal Machining
- Plastic Machining
- Powder Metallurgy Mold
- Die Casting
- Parts Gallery
- Auto Metal Parts
- Machinery Parts
- LED Heatsink
- Building Parts
- Mobile Parts
- Medical Parts
- Electronic Parts
- Tailored Machining
- Bicycle Parts
- Aluminum Machining
- Titanium Machining
- Stainless Steel Machining
- Copper Machining
- Brass Machining
- Super Alloy Machining
- Peek Machining
- UHMW Machining
- Unilate Machining
- PA6 Machining
- PPS Machining
- Teflon Machining
- Inconel Machining
- Tool Steel Machining
- More Material