The key to multi-material 3D printing: functional graded materials
"Multi-material" is a buzzword in the 3D printing industry. In terms of desktop 3D printers, it has been possible to print with multiple materials in one version, but industrial 3D printing also has many multi-material developments. This includes composite materials such as fiber reinforced Polymers. But Dr. Kevin Eckes, a research and development engineer at Aerosint, said that the "holy grail" of composite materials is functional graded materials (FGM). Eckes introduced to us Aerosint's unique method of multi-material powder bed 3D printing, and they are on Medium A more in-depth perspective is shared in the shared content. He recently shared with us his latest work on FGMs.
"Different from traditional composite materials, in traditional composite materials, reinforcement materials are distributed throughout the matrix material. FGMs are composite materials in which two materials are connected together through a gradual interface to avoid obvious differences between the two bulk materials. Boundaries," Eckes explained. "The purpose of creating this gradient is to distribute thermal and mechanical stresses over a larger volume, otherwise these stresses will be concentrated on a clear material boundary and cause cracks or breakage of the part."
Due to its failure resistance, FGM is very useful in extreme environments of high temperature, chemical or mechanical stress, and single-material parts may fail. An example of an FGM part is a metal-on-ceramic plate, where two materials counteract each other's weaknesses and enhance each other's strengths. The ceramic itself is hard, chemical and heat resistant, but it is also brittle and has low impact toughness. On the other hand, metal has high impact toughness, but it is easily corroded by strong acids and alkalis, and its mechanical properties are damaged when heated. However, putting these two materials together, they are almost indestructible.
Eckes said: "The metal-to-ceramic FGM can withstand the high temperature and harsh chemical environment of the ceramic surface, while maintaining the overall strength and resistance to brittle fracture through metal reinforcement."
Researchers at Japan's National Aerospace Science and Technology Laboratory first began to use cermet FGM in an attempt to create an effective and durable thermal barrier for reusable space vehicles. They found that a plate composed of a nickel-based superalloy and a composition gradient layer of stabilized zirconia on a nickel-based superalloy substrate can withstand a thermal gradient of more than 1000°C without cracking. Under the same conditions, 100% nickel superalloy is coated with 100% zirconia and chromium alloy as the relaxation layer to have thermal fatigue properties.
Metal-to-metal FGM is also very useful. For example, steel-copper FGM combines low-cost and high-strength steel with the high thermal conductivity and electrical conductivity of copper. In a recent example, the researchers created an injection molding tool that has a steel molded surface and a bulk copper body connected to a proprietary buffer layer material. Due to the high conductivity of copper, the mold cooling time is shortened by 10 seconds, and the overall mold cycle is shortened by 26%. The company estimates that increasing productivity can save them approximately $60,000 per year.
There are also polymer-to-polymer FGMs, where rigid and flexible polymers can be combined, such as a rigid arm with flexible joints in a manipulator, or wear-resistant polymers can be joined to tough polymers used for non-metallic bearings or moving parts .
“Most of the methods described in the research literature for creating FGM can only create 1D gradients, which are only suitable for a limited number of applications, such as durable thermal barriers,” Eckes continued. "To create multi-material parts and FGM with full 3D freedom, we need to perform voxel-level spatial control on the material layout. Several AM technologies currently on the market have this composition control capability, but they are mainly oriented toward prototype manufacturing. Or disposable parts manufacturing."
Aerosint specializes in multi-powder deposition, where powder voxels can be selectively transferred from a rotating drum to a build surface. Although Aerosint has theoretically demonstrated two types of powder deposition so far, many materials can be patterned. The material can be metal, polymer or ceramic, as long as the fluidity and particle size distribution of the powder are compatible with the process.
"The most fundamental challenge in our process is bi-material integration or sintering," Eckes said. "The melting temperature or sintering temperature of the two materials of eutectic sintering is very different, and there are obvious physical limitations. Nevertheless, many researchers have proved metal-metal and metal-ceramic co-sintering by carefully selecting materials with compatible properties. These combinations are not limitless, but we think they are rich enough to create a series of useful FGMs."
According to Eckes, the combination of multi-powder deposition and dual-material co-sintering is one of the most effective ways to achieve high-efficiency and rapid multi-material 3D printing. Aerosint is establishing partnerships with research institutions and scholars who have expertise in material co-sintering and metal and ceramic 3D printing.
Link to this article: The key to multi-material 3D printing functional graded materials
Reprint Statement: If there are no special instructions, all articles on this site are original. Please indicate the source for reprinting:https://www.cncmachiningptj.com
PTJ® is a customized manufacturer that provides a full range of copper bars, brass parts and copper parts. Common manufacturing processes include blanking, embossing, coppersmithing, wire edm services, etching, forming and bending, upsetting, hot forging and pressing, perforating and punching, thread rolling and knurling, shearing, multi spindle machining, extrusion and metal forging and stamping. Applications include bus bars, electrical conductors, coaxial cables, waveguides, transistor components, microwave tubes, blank mold tubes, and powder metallurgy extrusion tanks.
Tell us a little about your project’s budget and expected delivery time. We will strategize with you to provide the most cost-effective services to help you reach your target,You are welcome to contact us directly ( sales@pintejin.com ) .
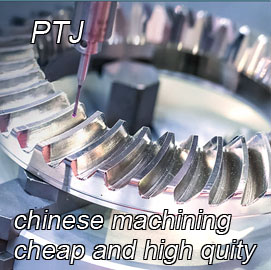
- 5 Axis Machining
- Cnc Milling
- Cnc Turning
- Machining Industries
- Machining Process
- Surface Treatment
- Metal Machining
- Plastic Machining
- Powder Metallurgy Mold
- Die Casting
- Parts Gallery
- Auto Metal Parts
- Machinery Parts
- LED Heatsink
- Building Parts
- Mobile Parts
- Medical Parts
- Electronic Parts
- Tailored Machining
- Bicycle Parts
- Aluminum Machining
- Titanium Machining
- Stainless Steel Machining
- Copper Machining
- Brass Machining
- Super Alloy Machining
- Peek Machining
- UHMW Machining
- Unilate Machining
- PA6 Machining
- PPS Machining
- Teflon Machining
- Inconel Machining
- Tool Steel Machining
- More Material