What is the market prospect of special rubber for vehicles?
1. The development status of my country's special rubber for vehicles
With the development of the automobile industry, the demand for special rubber for automobiles is booming. At present, my country's special rubber localization rate is not high, and it relies heavily on imports. Related domestic enterprises and research institutes are actively tackling key problems and making breakthroughs in some areas. So, what is the development status of my country's automotive special rubber industry? Where is the focus of research and development? How will the pace of localization be accelerated? The editor of Xianji.com will take you to find out.
At present, due to the continuous improvement of automobile performance and the continuous increase of the ambient temperature of automobile parts, the development and application of high-performance new raw materials with excellent oil resistance and high temperature resistance has become an important issue for the automobile rubber parts production industry. However, my country's special rubber relies heavily on imports, and it is urgent to increase research efforts to change this status quo.
New working conditions call for special glue
Automobile special rubber is mainly used in gearboxes, engines, fuel, transmission, and air-conditioning systems. It can meet the requirements of high performance, low energy consumption, low emissions, low noise and long service life. It will develop in the direction of special adhesives with excellent properties.
According to reports, with the development of automobiles in the direction of high performance, low fuel consumption, low emissions and low noise, and long service life, the structure and working conditions of automobiles have changed. For new devices such as fuel injection and turbocharging, the hose materials used in them must be able to withstand higher temperatures. Ordinary natural rubber, styrene butadiene rubber and butadiene rubber cannot meet the requirements for use under high temperature conditions. High temperature resistance must be adopted. Of special rubber materials.
At the same time, automobile fuels are also diversified. Fuels with high aromatic content, alcohol-containing blended fuels, bio-based fuels, peroxide acid gasoline, etc. are in use. Adding a certain amount of alcohols to fuel oil can increase the octane number of the fuel. The rubber swells severely, and the oil resistance is greatly reduced. The additives in the gear oil can easily cause the aging of the rubber material, resulting in the hardening of the sealing product, the decrease of the elasticity, and the failure.
Ren Wentan, a professor at Shanghai Jiaotong University, believes that in oxyfuel, biodiesel and mixed fuel systems, traditional fuel-resistant rubber sealing materials are no longer applicable, and new special rubbers can perfectly replace traditional rubber.
Performance defects need to be improved
The types of automotive special rubbers mainly include fluorine rubber, silicone rubber, acrylic rubber, hydrogenated nitrile rubber, etc. Although these rubbers can replace some traditional rubbers, there are still some defects in performance that need to be overcome. For example, fluororubber has strong resistance to high temperature and corrosion, but its raw rubber has low viscosity and is difficult to mix with other materials. Silicone rubber has excellent mechanical strength, but its oil resistance and tearing properties still need to be improved.
Ren Wentan said that only by improving the performance defects of special rubber itself can it be promoted. Silicone rubber needs to improve tensile strength, tear strength, and oil resistance; fluororubber needs to improve low temperature resistance, low hardness, and low viscosity; acrylic rubber needs to improve low temperature resistance and compression set performance. At the same time, when special rubber is compounded with other materials, nanomaterials are often used as special rubber reinforcing fillers, but nanomaterials cannot be dispersed in a nanometer state in some special rubbers, and they aggregate in clusters and cannot be used normally.
In addition, environmental protection issues during processing and use of special rubber compounds, such as polycyclic or fused-ring aromatic hydrocarbons in carbon black, heavy metals in inorganic fillers, vulcanization activators, volatiles in the vulcanization process, heavy metal content and aromatic compounds in rubber The proposed content restriction is also the focus of current formulation researchers.
Independent innovation and development of new products
At present, some new varieties of special rubber have appeared abroad, such as copolymerized fluorosilicone rubber, ammonia-based high fluorine-containing ternary polymerized fluororubber, and so on. The application prospects of these new special rubbers are very broad, but they cannot be produced in China due to foreign patented technologies.
Deng Tao, a professor at Qingdao University of Science and Technology, believes that my country’s current automotive-specific special rubbers have few varieties and specifications and cannot meet the needs of automotive rubber. Therefore, it is urgent to carry out technological innovation and develop high-performance new products. "The development of my country's new special rubber requires more accurate design methods and more precise manufacturing processes. Through the application of simulation technology, the relationship between the performance of the semi-finished rubber and the performance of the product can be obtained more accurately, so as to carry out a more optimized design. Significantly improve product performance and research and development efficiency." Deng Tao said.
According to the reporter's understanding, Qingdao University of Science and Technology is currently developing NBR/EPDM blended modified materials, which can withstand high and low temperatures, oil resistance, and ozone resistance. Industry experts pointed out that there is still a long way to go for the development of special rubber for vehicles in my country. Only through continuous technological innovation and product innovation can the gap with foreign countries be reduced. In the future, the combined use of rubber and the modification of rubber and plastic can be used as the development direction of special rubbers, such as NBR/PVC, FKM/NBR, FKM/ACM, etc., to make up for the shortcomings of traditional rubber and expand the scope of application.
High demand for special rubber for vehicles
With the upgrading of the automobile market and the rise of domestic brands, my country's automobile industry is in a period of shifting and increasing speed. Vehicles have put forward higher requirements on the performance and quality of rubber products, and rubber parts need to be greatly improved in heat resistance. , Cold resistance, oil resistance, aging resistance and other indicators.
The original rubber accessories made of general-purpose rubber can no longer meet the current requirements, and special rubber must be used instead.
"Special rubber for vehicles refers to rubber with the characteristics of high temperature resistance, oil resistance, ozone resistance, aging resistance and high air tightness. It is mainly used for special occasions that meet certain special requirements." Zhao Hongguo, Senior Engineer, PetroChina Lanzhou Chemical Research Center Say. It is understood that special rubber products for automobiles are important parts of automobiles, and various rubber products for automobiles are not only large in quantity but also demanding. At present, each car uses 400-500 special rubber parts, weighing about 40kg (excluding tires), accounting for 4%-5% of the entire vehicle, and its output value accounts for 6% of the total output value of auto parts.
Industry insiders said that special synthetic rubber for vehicles has excellent performance and has always been the darling of the market with high prices. New technologies have promoted the rapid development of special rubber. The amount of special synthetic rubber used in vehicles has increased year by year, and new special rubber materials have been continuously developed. At present, the consumption of special rubber in the automobile industry has reached 70%-80% of the total consumption of non-tire rubber products.
Most varieties rely on imports
Zhao Hongguo said that due to the relatively few varieties and specifications of special special rubber for automobiles in my country, the unstable quality and poor technical indicators, it cannot meet the demand for high-end special rubber for automobiles. In particular, some high-end special rubber products used in imported models cannot be produced in China and can only rely on imports.
Fluorine rubber is one of the representatives. It is understood that fluorine rubber has excellent properties such as odorless, non-toxic, non-combustible, heat-resistant, oxidation-resistant, oil-resistant, and chemical-resistant, and is used in engine crankshaft front oil seals, crankshaft rear oil seals, valve stem oil seals, and engine diaphragms Wait. However, due to the rising price of domestic fluororubber, many users have to import from abroad. Every year, China needs to import about half of fluororubber products from abroad to meet the needs of the development of the domestic automobile industry.
At the same time, acrylic rubber and EPDM rubber, as special rubbers with excellent performance, are also imported in large quantities every year. According to reports, acrylic rubber can be used to produce dozens of auto parts, and it has become a sealing material that has been developed and promoted by the auto industry in recent years. It is mainly used to manufacture various skeleton oil seals, such as crankshafts, gearboxes, transmission shafts and other parts of the oil seal; Various heat-resistant gaskets, sheaths, hoses, etc. It is estimated that the current domestic automobile industry's annual demand for acrylic rubber will reach around 20,000 tons. However, due to the fact that none of the acrylic rubber devices in my country have reached economic scale, they are far from meeting the needs of the domestic market. More than half of the acrylic rubber used in the production of auto parts needs to be imported.
Among the special rubbers for automobiles, EPDM rubber is the most consumed type of rubber, mainly for manufacturing door and window sealing strips, radiator hoses and other parts. my country's EPDM rubber synthesis technology and product application technology still need to be further improved, product quality still needs to be improved, and it needs to rely on imports to meet the needs of the domestic market.
Research needs to be strengthened
The industry believes that there are three reasons for the serious dependence on imports: one is that China is not able to produce new types of rubber; the other is that my country's new special rubber output is small, the production has not yet formed a large scale, and the products have not been serialized, and The quality also needs to be improved; thirdly, the application research on new types of rubber is not enough, and enterprises lack the awareness and ability to actively use new raw materials to improve product quality and production technology, and most of the research work is still on the application of existing raw materials. Discussion. To a certain extent, this limits and affects the development of China's automotive rubber products towards high performance.
Xu Dianhong, a senior engineer at PetroChina's Lanzhou Chemical Research Center, said that with regard to high value-added automotive rubber products, China has to work hard on key high-tech, sophisticated, and cutting-edge technologies in response to the problem of relying heavily on imports to meet domestic demand. Develop special rubbers suitable for special accessories, such as special rubbers for auto parts with high temperature resistance, dynamic performance, harsh use conditions, and excellent compression and permanent deformation performance, so that the performance of rubber accessories can meet the requirements of automobiles.
At the same time, through the introduction of capital, technology and equipment, the production of new rubber species can be scaled, serialized, and high-performance, providing new rubber species series with high output, good performance, stable quality and complete varieties for the production of automotive rubber parts. Gradually get rid of the dependence on imports of new rubber species.
2. Classification of automobile rubber products and their role in automobiles
The rapid development of China's automobile industry has promoted the development of other related supporting industries in my country, especially the rubber industry. In the past few years, automotive rubber products have developed into a unique and specialized product industry. Automobile rubber products are an indispensable and important component of automobile accessories. There are about 100-200 kinds of rubber products installed on each car, and about 200-500 rubber parts are used. Except for tires, it varies with different specifications of cars. The consumption of rubber materials is about 15-60 kilograms, and automobile rubber products (excluding tires) account for about 6% of the total cost of automobiles. There are about 1,000 varieties of non-tire rubber products for the automotive industry, with more than 8,000 specifications. According to statistics, the automobile industry occupies more than 70% of the global annual consumption of raw rubber, of which tires occupy 60%, and automobile rubber products and accessories occupy 40%.
High speed, safety, comfort, energy saving and environmental protection are the goals pursued by contemporary automobiles. With the development of automobile modernization, the requirements for automobile rubber products are becoming stricter and more demanding. Not only are rubber materials with various special properties required to meet the new technical requirements of automobiles, but also rubber materials are required to have higher physical and mechanical properties, such as It is resistant to aging, high and low temperature, new fuel oil and excellent dynamic fatigue performance, durable service life, etc. In fact, every high performance of a modern automobile has to rely on the technical progress of rubber products to provide guarantee. The performance and quality of automobile rubber products play an extremely critical role in improving the quality of the entire automobile. It is worth pointing out that the role played by rubber products is always an accessory, but this accessory always controls the technological progress and technical level of the host. Therefore, it can be said that the technology and quality of automobile rubber products can basically reflect the technical level of the entire automobile.
1. Classification of automobile rubber products and their role in automobiles
Rubber tires are called the two legs of a car, and the important role of tires in a car is self-evident. Tire is the rubber product that consumes the largest amount of rubber in the rubber industry. Therefore, in the rubber industry, tires are often separated from rubber products into a special variety. Among auto parts, rubber tires are a special kind of parts.
Automobile rubber products can be divided into seven categories: tires, sealing products, shock-absorbing products, safety products, tape products, hose products and other products such as wipers, mudguards, adhesives, sealants and interior products.
1.1 Tires
Car tires play the role of carrying the weight of the car's own weight, the full weight of the people and the goods on the car, and also play the role of making the car forward, reverse, turn and brake. The safety, comfort, and driving control performance of automobiles depend to a large extent on the high performance and high quality of tires.
Rubber tires have a history of 160 years. As early as 1845, the British R. W. Thomso put a rubber tube on the wooden wheel, thereby reducing the rolling resistance of the wheel and reducing the vibration, but this early rubber tire was very popular at that time. Of course, this should be attributed to the excellent properties of rubber materials. Until 1888, the British J. B. Dunlop invented the pneumatic tire. In the next one hundred years, with the development of the automobile industry, rubber tires have undergone several generations of product development, renewal and progress. The tire frame materials have developed from cotton cord, rayon to nylon cord bias tires. To today’s steel radial tires.
Mankind’s invention of pneumatic tires effectively promoted the development of automobiles. Because the pneumatic tire has excellent cushioning and shock absorption performance, it significantly reduces vibration, making the car operation safer, more comfortable to ride, and can greatly increase the driving speed of the car. With the continuous progress of rubber materials, formulation technology, manufacturing equipment and manufacturing processes, the safety and life durability of automobile tires have been greatly improved. For example, in 1900, the mileage of each tire was only 800km; by 1978, the mileage of each tire had reached 60,000 km; in the 21st century, the mileage of each tire was no less than 140,000 km, even 20 Million km. With the rapid construction and use of expressways, the speed of vehicles has increased substantially, from tens of km/h to 100 km/h, 140 km/h or even 200 km/h.
1.2 Sealed products
Sealing products are divided into three categories: O-rings, skeleton oil seals and sealing strips. O-rings and skeleton oil seals are installed on the engine, gearbox, car main shaft and hydraulic pneumatic transmission system to prevent lubricating oil, hydraulic oil and other liquid leakage or gas leakage, ensure the normal operation of each component system, and prevent external sand particles Dust and impurities enter the system and affect the normal operation of the machine. O-rings and skeleton oil seals are mainly used for the sealing of rotating shafts or reciprocating shafts. According to the structure, the skeleton oil seal can be divided into inner skeleton oil seal, outer skeleton oil seal, semi-exposed skeleton oil seal, sealing lip oil seal, oil seal with auxiliary lip and combined oil seal, etc.; according to the installation position in the car, it can be divided into crankshaft front oil seal and crankshaft rear oil seal. , Gearbox oil seals, cam box oil seals, wheel housing oil seals, axle shaft oil seals, pneumatic guide rod oil seals and shock absorber oil seals, etc. Sealing strips are mainly used in automobile doors and windows, trunks, engine hoods, etc., to play the role of sealing, wind blocking, rain blocking, shock absorption and sound insulation. According to the structure, it can be divided into pure rubber sealing strip (also can be divided into sponge glue and dense glue) and composite sealing strip (rubber/metal frame composite strip, two or more rubber composite strips and rubber plastic composite strips).
1.3 Shock absorption products
Rubber shock-absorbing products are mainly installed in the engine, body, air conditioner and cabin suspension system. It is mainly used to reduce the vibration and noise when the car is driving, and to improve the stability, safety and comfort of car handling. With the continuous improvement of the comprehensive performance of modern automobiles, higher and higher requirements are put forward on the performance and quality of rubber shock-absorbing products. The main requirement is that shock-absorbing products have excellent shock-absorbing damping performance, anti-dynamic fatigue performance and long life durability. Automobile rubber damping products mainly include air springs, engine front and rear suspension pads, flexible couplings, and various shapes of rubber bushes, gaskets, etc. Special shock absorbers with excellent performance are also installed in each tire support on premium cars.
1.4 Safety products
Automobile rubber safety products play a role in braking reliability, driving safety and personal safety in automobiles. Safety products mainly include brake film (diaphragm), leather cups, brake pads, airbags and bumpers.
The brake film and the leather cup are directly related to the safety of the car. When the car encounters an accident during the driving, the car will be quickly decelerated or even stopped to ensure the safety of the vehicle and personnel. Airbags are rubber products that provide safety for vehicle personnel when a vehicle is hit by an accident. The bumper is used to reduce the impact force when the car is in a collision.
1.5 Hose products
Hose products are used in the three major parts of the chassis, engine and body. They are used for the seven systems of oil, gas, drive, control, braking, cooling and heating, and play the role of oil supply, gas supply, water supply and power transmission. The types of hoses include fuel hoses, water delivery hoses, brake hoses, vacuum hoses, air conditioning hoses, radiator hoses, power steering hoses and special-shaped branch hoses.
1.6 Tape products
Tape products are mainly used in automobiles to transfer torque power and speed, and transfer power from the power source engine to the place where power is needed. Installed in cooling fans, cooling water pumps, brake compressors, booster pumps, air conditioning systems, and steering systems. Tape products are divided into V-belt (also divided into ordinary V-belt and V-ribbed belt) and synchronous belt (toothed belt). According to the structure, V-belts are divided into cutting belts and cloth-covered belts. The V-belt is characterized by high speed and large transmission power. Synchronous toothed belts are used for gas ignition of automobile engines, and their use conditions are high speed, high transmission power and high temperature.
1.7 Other products
Such rubber products include automobile rubber sheets (in-car rubber sheets and fenders), automobile interiors and adhesives, sealants, wiper strips, etc. Floor glue is used to lay the ground in the car, anti-vibration and anti-skid. The wiper strip is used to wipe off the rain and snow on the windshield in rainy and snowy weather to ensure the driver's sight, normal operation and normal driving of the vehicle. Adhesives are used for the bonding of automotive interior materials and the protection of the bottom of the car.
2 The status quo and development trend of my country's automotive rubber products
2.1 Tires
In recent years, as cars have gradually entered the family, it has stimulated the rapid development of my country's automobile industry and promoted the development of the automobile supporting industry and the rubber product industry. Obviously, rubber tires are the first to bear the brunt.
Due to the high speed of automobiles, rubber tires have transformed from bias tires to radial tires. Radial tires are the development direction of my country's tire industry and are the key models supported by the state. Beginning in 2001, domestic tire factories in my country have been carrying out infrastructure and technical transformations around radial tires, which have developed rapidly and are very successful. In 2004, my country’s tire output reached 210 million, of which 109 million radial tires, with a radialization rate of 52%. In addition to meeting the domestic market demand, nearly one-third of the output of tires has entered the international market. In 2005, my country’s tire output reached 230 million, of which 130 million were radial tires, with a radialization rate of 56%. It is predicted that by 2010, my country’s tire production will reach 300 million, of which 210 million radial tires, with a radialization rate of 70%. Radial tires will account for about 85% of car tires. By 2015, we will strive to achieve 95% of car tires.
In 2004, my country’s tires consumed 2.2 million tons of raw rubber. In 2005, rubber consumption reached 2.43 million tons, an increase of 10.5%. Among them, natural rubber accounts for about 56.6%, synthetic rubber accounts for about 43.4%, synthetic rubber is mainly styrene-butadiene rubber and butadiene rubber (tyre), as well as butyl rubber, chlorinated butyl rubber (inner tube). Due to the limited natural rubber resources in my country, the future development direction should appropriately increase the proportion of synthetic rubber used. The main added synthetic rubbers are styrene butadiene rubber and butadiene rubber. However, since the comprehensive properties of these two synthetic rubbers are not comparable to those of natural rubber, excessively increasing the application ratio of these two synthetic rubbers will reduce the quality of tires. In the future, the physical properties of these two kinds of rubbers should be improved or new varieties should be developed.
2.2 Sealed products
In recent years, through the introduction of foreign advanced technology, equipment and technological transformation in my country’s automobile rubber products industry, a number of key enterprises with larger production scales and higher professional levels have emerged, gradually forming a relatively complete industrial system that can basically satisfy And meet the needs of my country's automobile industry.
At present, there are more than 30 skeleton oil seal plants with a certain scale and level in China, with a total production capacity of about 200 million pieces. At present, domestically, it can produce automobile-specific skeleton oil seals with various structures including internal and external skeleton oil seals, pressure-resistant oil seals, and main lip with oil-return line fluid dynamic oil seals, which can meet the needs of the domestic automobile market. However, due to the high speed of automobiles and the addition of fuel additives, the operating temperature, medium resistance and accuracy of the oil seal have been improved day by day. For example, the linear speed of the rear oil seal lip of some car crankshafts can reach 200 m/s, and the lip temperature can reach 250°C. The structure and material of the original oil seal can no longer meet the requirements of use. Fluorosilicone rubber, acrylic rubber and fluororubber are commonly used in foreign automobile engine oil seals. The NBR/PTFE composite oil seal can make the life of the oil seal reach 4000-4500h, that is, the mileage can reach 130,000 km-180,000 km.
However, my country's automobile oil seals are still dominated by nitrile rubber. Although a few manufacturers can produce fluorine rubber and acrylic oil seals, the output and quality cannot keep up with the needs of the automobile industry, and their service life is less than 100,000 km. Oil seals for key parts of high-end cars, such as crankshaft rear oil seals and automobile guide rod oil seals, still rely on imported parts, and the localization rate is very low. For the skeleton oil seal, further improving the heat resistance, dynamic fatigue resistance and compression set resistance of the rubber compound, improving the level of tooling and automation, and improving the accuracy of mold processing are all future tasks. The main material of the oil seal will be widely used in fluorosilicone rubber, chloroether rubber, hydrogenated nitrile rubber and acrylic rubber.
There are more than 60 manufacturers of sealing strips in my country, with 49 production lines for various types of automotive sealing strips, with a total annual production capacity of 200 million meters.
Sealing strip is one of the fastest-growing industries in my country's rubber products in recent years. Regardless of the output, output value or profit, there has been a substantial increase, and a professional system has basically been formed. The production plants have introduced the production technology, equipment and testing instruments of the Italian Saya Seals Company. The technology and product quality are equivalent to the international level in the 1990s. They can design and develop products on their own to basically meet the needs of the domestic car industry. The rubber varieties are basically EPDM rubber. The future development direction will use TPE as the sealing tape, TPV as the glass guide groove, and adopt the new technology of multi-face flocking and extrusion laminating.
2.3 Shock absorption products
my country has more than 20 large-scale rubber shock-absorbing products factories with a production capacity of about 70 million pieces, which can basically meet the needs of domestic automobile production and maintenance and replacement.
At present, advanced foreign countries have successfully developed a new generation of rubber shock absorbers such as liquid-sealed shock absorbers, electronically controlled shock absorbers, and torsion shock absorbers. Such products are still in the development stage in China. my country's automobile shock-absorbing products still mainly use natural rubber, and the combination of natural rubber and butadiene rubber or butadiene rubber. The development direction of materials should be ethylene propylene diene rubber, butyl rubber and other rubbers with good heat resistance and excellent damping properties. The development of new-type shock-absorbing materials that are more heat-resistant and resistant to dynamic fatigue and the development of liquid-sealed shock absorbers are research topics that my country should invest more in in the future.
2.4 Safety products
There are more than 30 manufacturers of brake coatings (diaphragms) and brake cups for automobiles in my country. After years of transformation, the product performance basically meets the requirements of the automobile industry. The service life of domestically produced high-strength rubber diaphragms has reached the technical mark of 1 million times. The membrane production capacity is 35 million pieces, and the diaphragm production capacity is 15 million pieces. The main raw rubber used is natural rubber or a combination of natural rubber and synthetic rubber. In the future, high-strength rubber diaphragms such as EPDM rubber and thermoplastic elastomer TPE should be further developed and applied.
The production of airbags in my country has just started, with only 6-7 manufacturers, with a total production capacity of about 200,000 sets/year. The National Automobile Safety Law stipulates that cars with a total weight of less than 2.5 tons (M1 category) must undergo a crash test before being listed. All cars in the future must meet the standards and must be equipped with safety capsules. Airbags are generally made of nylon and made of neoprene. Looking forward to the next development direction is the use of thermoplastic elastomers to manufacture airbags.
2.5 Hose products
Automotive hoses have grown at a rate of about 25% in recent years. There are more than 20 domestic automotive hose plants of a certain scale, with a total production capacity of 200 million standard meters. Mainly braided hoses and winding hoses, the proportion of resin composite hoses including brake hoses and cooling water hoses is increasing; short fiber hoses are valued due to their simple process and good performance. From the perspective of rubber materials, it has developed from a single type of rubber in the past to using different types of rubber in the inner, middle and outer layers to adapt to different working environment conditions, generally composed of 2-3 different rubbers. In recent years, the development of domestic automobile hoses has begun to take shape. Many companies have introduced advanced foreign technology and equipment, and the quality of their products has been greatly improved. However, compared with foreign countries, there is still a big gap, and low- and mid-range products can meet market requirements. High-end products such as fuel pipes, thin braided hoses, heat-resistant pipes, etc. still rely on imports. The matching rate of domestic cars of this kind of products is only 40%, and the matching rate of high-end cars is only 5-10%. In addition to nitrile rubber, the rubber material also uses nitrile rubber/polyvinyl chloride blends, and further uses hydrogenated nitrile rubber, chloroether rubber, chlorosulfonated polyethylene and EPDM rubber.
2.6 Tape products
The production of transmission belts for cars in my country, especially timing belts, started late. After the reform and opening up, some joint ventures have successively introduced foreign advanced technology and equipment and developed corresponding products in order to cooperate with the introduction of car localization, which basically met the demand for cars; however, there is still a certain gap in product quality and performance compared with similar foreign products. . The production process of the V-belt for automobiles has replaced the edging belt with the trimming belt. In terms of materials, hydrogenated nitrile rubber is mainly used abroad; chloroprene rubber is still the main domestic rubber. A few use EPDM and chlorosulfonated polyethylene elastomers. Hydrogenated nitrile rubber cannot be used because of the high price. , Therefore, the service life of the domestic V-belt is only about 100h. Foreign V-belts can be used for 180,000 km, which can be synchronized with car overhaul. There are about 300 automobile transmission belt manufacturers in my country, with a production capacity of 500 million standard meters of V-belts and 20 million synchronous belts.
2.7 Other products
Automobile wiper rubber strips are one of the more problematic varieties of automobile rubber products in my country. The main problems are high noise, intolerance to wear and poor wiping efficiency. The main material of domestic wiper strips is neoprene. Foreign countries have conducted in-depth research on materials and structures. For example, use EPDM or silicone rubber to replace neoprene, add solid lubricants to the rubber compound, or spray wear-resistant materials on the surface. The quality of automobile wiper strips has attracted the attention of the Chinese people, and some manufacturers have launched relevant research and achieved good results.
Automobile sealant is mainly used for sealing between car body, door steel plate welds and connecting parts. Adhesives for automobiles mainly include PVC hot melt adhesives, asphalt primers and neoprene adhesives.
3. Ideas to improve the technical level of my country's automotive rubber products
3.1 First of all, the government must pay great attention to it, and guide enterprises to increase investment in technological research through policy support.
Relevant government departments should pay attention to the quality of auto parts as a key factor related to car quality. Earnestly organize domestic technical elites in relevant industries to selectively target several key technologies for research and research. We can learn from the experience model of "Guangdong-Hong Kong key material technology research" adopted by Guangdong Province in recent years. Organized by the Provincial Department of Science and Technology, experts from enterprises, research institutes, and universities will screen, demonstrate, establish, and bid on major materials and technologies encountered in the current economic construction of the province and Hong Kong. The research funding is partly allocated by the provincial government and related functional departments, and the company will develop a certain proportion of the corresponding funds, which will be jointly developed by the winning enterprise and the institution. After several years of experimentation, the results have indeed been achieved.
3.2 Carry out the development and research of urgently needed special raw materials, and change the status quo of "cooking without rice".
3.2.1 Varieties of Synthetic Rubber
High-quality EPDM used for composite sealing strips and brake skins, fluororubber varieties for skeleton oil seals with engine resistance to high temperature, high pressure, abrasion resistance and good adhesion above 200℃, fluorosilicone rubber, wear-resistant acrylic rubber, hydrogenated carboxyl group Nitrile rubber, oil-resistant silicone rubber and acrylic rubber with excellent low-temperature properties, etc.
3.2.2 New vulcanizing agents, additives and framework materials
To catch up with advanced international countries, develop a new generation of environmentally friendly crosslinking agents, accelerators and additives, high-strength framework materials such as polyester with excellent adhesion, high-strength glass fiber, and aramid with good stability.
3.3 The enterprise unites scientific research institutes and institutions of higher learning to organize capable scientific research forces to focus on accelerating the development of high-precision products in the short-term, and increase the rate of localization of high-end vehicles.
1. Car crankshaft high-speed oil seal and crankshaft oil seal, meet 8000Km, temperature 250℃, working life 4000-5000h;
2. Liquid-sealed composite shock absorber, torsion shock absorber, electronic shock absorber, temperature resistance 300℃;
3. Heat-resistant fuel hose and thin-walled hose (wall thickness ≤ 2mm);
4. Multi-channel special-shaped hose;
5. High-strength rubber film, requiring high and low temperature resistance, and a life span of 50×10000 times at room temperature for normal operation.
Link to this article: What is the market prospect of special rubber for vehicles?
Reprint Statement: If there are no special instructions, all articles on this site are original. Please indicate the source for reprinting:https://www.cncmachiningptj.com
PTJ® is a customized manufacturer that provides a full range of copper bars, brass parts and copper parts. Common manufacturing processes include blanking, embossing, coppersmithing, wire edm services, etching, forming and bending, upsetting, hot forging and pressing, perforating and punching, thread rolling and knurling, shearing, multi spindle machining, extrusion and metal forging and stamping. Applications include bus bars, electrical conductors, coaxial cables, waveguides, transistor components, microwave tubes, blank mold tubes, and powder metallurgy extrusion tanks.
Tell us a little about your project’s budget and expected delivery time. We will strategize with you to provide the most cost-effective services to help you reach your target,You are welcome to contact us directly ( sales@pintejin.com ) .
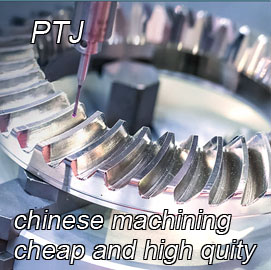
- 5 Axis Machining
- Cnc Milling
- Cnc Turning
- Machining Industries
- Machining Process
- Surface Treatment
- Metal Machining
- Plastic Machining
- Powder Metallurgy Mold
- Die Casting
- Parts Gallery
- Auto Metal Parts
- Machinery Parts
- LED Heatsink
- Building Parts
- Mobile Parts
- Medical Parts
- Electronic Parts
- Tailored Machining
- Bicycle Parts
- Aluminum Machining
- Titanium Machining
- Stainless Steel Machining
- Copper Machining
- Brass Machining
- Super Alloy Machining
- Peek Machining
- UHMW Machining
- Unilate Machining
- PA6 Machining
- PPS Machining
- Teflon Machining
- Inconel Machining
- Tool Steel Machining
- More Material