Six major factors of 3D printing cost reduction, a quick look!
Over time, the application of 3D printing has gone far beyond making prototypes. Now, the technology has taken a place in the manufacturing industry. For example, the Juno spacecraft built by Lockheed Martin and NASA is currently completing its mission in Jupiter orbit, carrying thirteen 3D printed waveguide supports. . Activated Research Co. uses 3D printing technology to develop a new design for its Polyarc gas chromatography catalytic microreactor, which can be put on the market in just 15 months. Raytheon uses 3D printing to manufacture control parts for rocket motors and fins. The production time is only a few hours instead of days.
According to reports, Boeing created the largest 3D printed product to date in 2016, a jig used to manufacture the 777 aircraft, setting a world record, and it is reported that its manufacturing time has been shortened by several weeks.
In these cases, the results include more features, lower weight, and lower manufacturing costs, and all three are common. The following six factors make these benefits possible:
1. Optimized design
Well-designed 3D printed parts follow many of the same rules as injection molding. These include the use of gradual transitions between adjacent surfaces. Eliminate huge differences in cross section and part volume. Avoid sharp corners that often produce residual stress on the finished workpiece. Note that the thin, unsupported walls will not print too high, or they may bend or warp. Surfaces with shallow angles tend to leave ugly "stepped" surfaces, which make them lack cosmetic features, so they need to be flattened as much as possible.
2. Abandon tradition
The most dramatic 3D printed part designs use the power of 3D to create "organic" shapes, such as honeycombs and complex matrices. Don't be afraid to use these shapes, only doing so will create lighter and stronger parts. You should also not be afraid to place holes (and many of them) in your design. With the development of traditional manufacturing, drilling holes in solid material blocks increases the cost and waste of parts. This is not the case in the 3D printing world, because more holes means less powder and less processing time. Remember, the 3D printed holes do not need to be circular. Generally, oval, hexagonal or free-form hole shapes will better suit the part design and are easier to print.
3. Consider the next steps in the design cycle
However, just because you can print parts with many holes, it doesn't mean you should print this way, especially if you plan to make many such parts in the future. Because 3D printing provides great design flexibility, there is no need to consider how to make parts after prototyping. Based on the example at the beginning of this design tip, more and more companies are finding 3D printing suitable for end-use parts, but as production increases, many parts will switch from printing to machining, molding, or casting. This is why it is very important to perform manufacturability (DFM) analysis early in the design cycle to ensure cost-effective production throughout the part life cycle.
4. Avoid secondary operations
Plastic parts produced with SLS do not require support structures during the production process, so post-processing is usually limited to painting, reaming, tapping holes, and machining key part features. On the other hand, direct metal laser sintering (DMLS) usually requires a large number of scaffold-like structures to support and control the movement of metal workpieces. Without them, the surface may curl and warp. This is especially true for cantilever geometries, such as a wide T-shape, which requires the construction of supports under the arms, which must be machined or polished, thereby increasing the cost. This story is similar to SL but not very compelling, where the cured resin bracket can be easily removed with a hand-held sander and some sandpaper. Where possible, parts should be oriented to reduce these protrusions and other unfriendly features.
5. Observe the tolerance
Designers and engineers should avoid "over-tolerance" parts, as this may force them to use thinner layers to build (increasing build time and cost), and often require secondary processing operations to meet excessive print sizes. Since 3D printing provides many opportunities to reduce the number of parts, there is no need to achieve ultra-precise fit between mating surfaces in any case. This is just another example of how this technology can reduce manufacturing costs.
Some parts produced with DMLS need to be sorted manually. Well-designed 3D printed parts can minimize post-production steps, thereby reducing cost and time.
6.Look at the big picture
3D printed parts may require more upfront costs, but don't let it frighten you. Using 3D printing, you can reduce the number of parts, reduce weight, improve structural integrity, reduce assembly costs, reduce internal channels for cooling or wiring, and other functions that cannot be achieved by traditional designs. Also, keep in mind that 3D printing does not require fixtures, molds, and other types of tools, thereby eliminating costs that may not be directly related to the price of individual parts. Focusing on the price tags of parts, rather than product features and "big picture", may allow you to design the same parts as before, thereby eliminating the opportunity to reduce overall manufacturing costs.
Link to this article:Six major factors of 3D printing cost reduction, a quick look!
Reprint Statement: If there are no special instructions, all articles on this site are original. Please indicate the source for reprinting:https://www.cncmachiningptj.com
PTJ® provides a full range of Custom manufacturer of precision fabricated parts made from aluminum parts, brass parts, bronze, copper parts, high yield alloy, low carbon steel investment casting, high carbon steel and stainless steel alloy. Capable of handling parts up to +/-0.0002 in. tolerance. Processes include cnc turning, cnc milling, laser cutting,.ISO 9001:2015 &AS-9100 certified.
Tell us a little about your project’s budget and expected delivery time. We will strategize with you to provide the most cost-effective services to help you reach your target,You are welcome to contact us directly ( sales@pintejin.com ) .
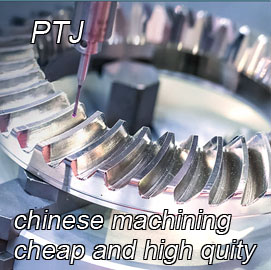
- 5 Axis Machining
- Cnc Milling
- Cnc Turning
- Machining Industries
- Machining Process
- Surface Treatment
- Metal Machining
- Plastic Machining
- Powder Metallurgy Mold
- Die Casting
- Parts Gallery
- Auto Metal Parts
- Machinery Parts
- LED Heatsink
- Building Parts
- Mobile Parts
- Medical Parts
- Electronic Parts
- Tailored Machining
- Bicycle Parts
- Aluminum Machining
- Titanium Machining
- Stainless Steel Machining
- Copper Machining
- Brass Machining
- Super Alloy Machining
- Peek Machining
- UHMW Machining
- Unilate Machining
- PA6 Machining
- PPS Machining
- Teflon Machining
- Inconel Machining
- Tool Steel Machining
- More Material