The international development trend of plastic extruder in my country
After more than 100 years of development, plastic extruders have derived from the original single-screw, twin-screw, multi-screw, and even non-screw models.
The plastic extruder (host) can be used with various plastic forming auxiliary machines such as pipe, film, holding material, monofilament, flat wire, strapping, extruding net, board (sheet) material, profiled material, pelletizing, cable coating, etc. Matching to form various plastic extrusion molding production lines to produce various plastic products. Therefore, plastic extrusion molding machinery is one of the widely used models in the plastic processing industry, no matter now or in the future.
In my country's plastic machinery market, as an important processing equipment, plastic extruders play a decisive role in the processing of straps, plates, films, pellets, profiled materials and other products. The development of extruder processing technology has always been the focus and hotspot of the development of the plastics processing industry. For a long time, the development of its processing technology has directly affected the development of the plastics processing industry.
After decades of technology accumulation and precipitation, my country's plastic extruder technology development has made certain breakthroughs. With the development of the plastic processing industry in the direction of extreme, precision, and high speed, the related plastic extruders also show the development characteristics of high efficiency, multi-function, and low energy consumption.
Modularization Specialization
Nowadays, as the development of plastic extruders becomes more and more perfect, different types of extruders with different functions have appeared in the plastic processing market. All kinds of extruders will inevitably be dazzling. Therefore, the factory adopted a modular production method for the extruder. This production method can not only meet the requirements of different plastic products, but also meet the special needs of different users, so that users can get the products they want in the first time. In addition, this production method can shorten the research and development cycle of new products and strive for a larger market share. The specialization in the production process allows each system module component of the extrusion molding equipment to be arranged for fixed-point production or even global procurement, which is very beneficial to ensuring the quality of the entire period, reducing costs, and accelerating capital turnover.
High efficiency and high speed
At present, the characteristics of high output and low energy consumption of plastic extruders have promoted its development in the direction of high efficiency and high speed. Take the same direction twin screw extruder as an example. The extruder uses a high-torque gear box. The performance of this type of gearbox is stable, with a longer life span and a larger load-carrying capacity. The gearbox specific torque can reach 14Nm/cm3, and the maximum output speed can reach 1800r/min. In addition, increasing the diameter of the screw can also increase the production capacity of the extruder. When the diameter of the screw is doubled, the production capacity of the extruder can be increased several times, thereby improving the production efficiency of the extruder.
Intelligent network
Nowadays, many plastic extruders in developed countries have been artificial intelligence, and modern electronic and computer control technology are generally used. The addition of intelligent technology can not only achieve high product accuracy, but also make the entire processing process more stable. Although my country's current extruder is not as intelligent as abroad, with the continuous innovation of technology, China's extruder has also achieved certain results in the field of intelligence. For example, the application of intelligent temperature control system and intelligent monitoring system for extruder.
In the future, my country's plastic extruders will continue to follow international development trends, innovate and upgrade their own technology, and strive to develop more efficient, stable, safe, and quality-preserving extruders in accordance with market needs.
Link to this article: The international development trend of plastic extruder in my country
Reprint Statement: If there are no special instructions, all articles on this site are original. Please indicate the source for reprinting:https://www.cncmachiningptj.com
PTJ® provides a full range of Custom manufacturer of precision fabricated parts made from aluminum parts, brass parts, bronze, copper parts, high yield alloy, low carbon steel investment casting, high carbon steel and stainless steel alloy. Capable of handling parts up to +/-0.0002 in. tolerance. Processes include cnc turning, cnc milling, laser cutting,.ISO 9001:2015 &AS-9100 certified.
Tell us a little about your project’s budget and expected delivery time. We will strategize with you to provide the most cost-effective services to help you reach your target,You are welcome to contact us directly ( sales@pintejin.com ) .
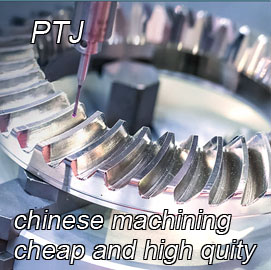
- 5 Axis Machining
- Cnc Milling
- Cnc Turning
- Machining Industries
- Machining Process
- Surface Treatment
- Metal Machining
- Plastic Machining
- Powder Metallurgy Mold
- Die Casting
- Parts Gallery
- Auto Metal Parts
- Machinery Parts
- LED Heatsink
- Building Parts
- Mobile Parts
- Medical Parts
- Electronic Parts
- Tailored Machining
- Bicycle Parts
- Aluminum Machining
- Titanium Machining
- Stainless Steel Machining
- Copper Machining
- Brass Machining
- Super Alloy Machining
- Peek Machining
- UHMW Machining
- Unilate Machining
- PA6 Machining
- PPS Machining
- Teflon Machining
- Inconel Machining
- Tool Steel Machining
- More Material