In addition to weight reduction, what other commercial values can not be ignored in the 3D printing dot matrix structure?
Grid-like truss bridges, honeycomb-like buildings, and porous bone tissue. The world we live in is full of various man-made or natural honeycomb lattice structures. Materials with a lattice structure have attracted people's attention due to their advantages in thermal, electrical and optical properties, and as potential lightweight materials. So in addition to the role of lightweight, are there other commercial values that are equally important but easy to be overlooked by us?
In this regard, Incase uses Carbon's 20 3D printing platforms to design and produce more advanced mobile device protection devices. This is the industry's first 3D printed new elastomeric complex structure design mobile device protection solution. It can be seen that in commercial products, buffer protection is so important, but we have been neglecting it. Let's take a closer look at the unusual business prospects of the lattice structure, especially the micro lattice structure.
The big use of micro-lattice structure
Boeing demonstrated the great potential of their unique 3D printed micro-lattice structural material in 2015, and Boeing believes that this is the lightest metal in the world. The research and development background of this material was started in 2011 by the Boeing subsidiary HRL Laboratory for the Defense Advanced Research Projects Agency (DARPA). The weight is lighter than plastic, the wall structure is a thousand times thinner than human hair, and the density is only 0.9 mg/cc. The structure is a metal array of interconnected hollow tubes, which makes it very resistant. Compressibility and high level of absorption.
The basic structure of this breakthrough metal structure created by HRL laboratory through 3D printing technology is a template formed by UV light curing polymer. Then, electroless plating is used to plate an ultra-thin layer of nickel on the template, and then the hot polymer template material is removed, leaving only a hollow metal structure. 99.99% of the metal structure is air, and the nano-solid structure accounts for only 0.01%. The thickness of the hollow tube wall is only 100 nanometers, which is 1,000 times thinner than a hair.
Boeing will use this ultra-light 3D printing material for non-mechanical parts such as aircraft walls and floors. This will greatly reduce the weight of the aircraft and improve the fuel efficiency of the aircraft. The unique structure of the material allows it to recover from a compression ratio of more than 50%, and has a very high energy absorption capacity. The Boeing video clearly shows the material being "crushed" and then returned to its original shape. Boeing claims that the structure can be used to safely absorb the impact of an egg falling from the 25th floor.
Dynamic behavior of dot matrix
Scientists from the United States Lawrence Livermore National Laboratory (LLNL) and other scientific research institutions have also conducted related research on 3D printing microlattice structure materials. In the research, the scientists used the impact load method to study the dynamic properties of the engineering lattice structure. The collaborative behavior of Chinese materials. There are two dynamic properties in the scope of research, one of which is compression property, and the other is the elastic property of the lattice structure.
Scientists can further manipulate the lattice structure through micron-level 3D printing technology to bring order and periodicity on the mesoscopic scale to these materials, beyond the disorderly distribution of the lattice structure designed by traditional methods. It can be seen that through 3D printing technology, people can realize the customized design of lattice materials, especially for the specific needs of the application, precisely design and manufacture special lattice materials.
Plastic dot matrix-disrupt the foam industry
3D printing company Carbon has stated that the complex and diverse grid structure of 3D printing a variety of elastomer materials will enable it to affect or even disrupt the current foam industry. In other words, although the current foam plastics still play a role in comfort and safety, Carbon believes that its customized 3D printing structure will replace part of the foam market with its unique advantages.
For industrial applications, the glass fiber reinforced polyurethane foam made by reaction injection molding has been used as structural parts for airplanes, automobiles, computers, etc.; while the foam made by filling polybenzimidazole with hollow glass beads is of high quality. Light and high temperature resistant, it has been used in spacecraft. In addition, high performance has become a new direction and hot spot in the research of foam plastics. High-performance foam plastics can be used as load-bearing structural materials in aviation, aerospace, transportation and other fields, such as the skeleton of satellite solar cells, the fairing of the front end of the rocket, the vertical tail of unmanned aircraft, the wing of the cruise missile, and the Large radome, etc.
Carbon believes that its 3D printing materials can partially replace the existing foam plastic market, including cushioning bottoms for running shoes and cushioning materials for helmets. This is mainly due to Carbon's ability to automatically generate a lattice structure according to user needs. More specifically, using Carbon's software, users can simply enter the design constraints of the part (such as weight and size) and the required mechanical properties to obtain lattice structural materials that meet their specific needs.
Metal lattice
Although the metal lattice structure does not have the advantages of the plastic lattice structure in terms of shock absorption, the complex metal lattice structure can provide excellent product performance-both in terms of efficiency and functionality. And it opens up a broad design space for the lightweight components, and can also improve heat transfer, energy absorption, insulation and improve connection performance.
When designing lightweight structural parts, it is necessary to combine the function realization of the entire part, and comprehensively consider factors such as void accuracy, void ratio, void shape, void size, pore distribution, and mutual connectivity. Lightweight structural parts are composed of basic structure, shape structure and ultra-light structure. In this process, the level of design ability is reflected. At this time, auxiliary design software came into being. It is understood that in this regard, in addition to established modeling software companies such as Autodesk's Netfabb software, and established companies focused on the 3D printing field such as Materialise, there are also some start-ups in the market, such as cloud-based complex lattices. The modeling software platform Betatype Engine brings great room for material technology, including shape gradual structure, creation of composite materials, foam sandwich panel structure, and other structural materials. Not only does the geometric complexity of freedom be carried to the extreme, it also brings great freedom to the designer.
However, although the lattice structure is very attractive and attractive, there are still some obstacles that make it difficult to use the lattice structure in the actual production of parts. A key challenge is to prove the performance reliability of the design, especially in terms of fatigue resistance. Due to the large number of surface and sharp intersections of the lattice structure, this brings stress concentration, and the actual application of batch parts cannot accept such events as possible failure.
So a related problem is how to verify the manufacturing quality. The complexity of the lattice structure makes it difficult to inspect by traditional methods. CT scans provide a solution, albeit somewhat time-consuming.
It is understood that domestic companies such as China Academy of Space Technology, Blite, and Xinjinghe are all exploring hardships. Despite the great challenges currently facing, we have reason to believe that one day, the lattice structure will occupy an important place in additive manufacturing.
Link to this article:
Reprint Statement: If there are no special instructions, all articles on this site are original. Please indicate the source for reprinting:https://www.cncmachiningptj.com
PTJ® provides a full range of Custom manufacturer of precision fabricated parts made from aluminum parts, brass parts, bronze, copper parts, high yield alloy, low carbon steel investment casting, high carbon steel and stainless steel alloy. Capable of handling parts up to +/-0.0002 in. tolerance. Processes include cnc turning, cnc milling, laser cutting,.ISO 9001:2015 &AS-9100 certified.
Tell us a little about your project’s budget and expected delivery time. We will strategize with you to provide the most cost-effective services to help you reach your target,You are welcome to contact us directly ( sales@pintejin.com ) .
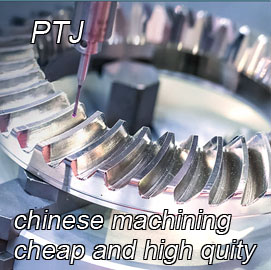
- 5 Axis Machining
- Cnc Milling
- Cnc Turning
- Machining Industries
- Machining Process
- Surface Treatment
- Metal Machining
- Plastic Machining
- Powder Metallurgy Mold
- Die Casting
- Parts Gallery
- Auto Metal Parts
- Machinery Parts
- LED Heatsink
- Building Parts
- Mobile Parts
- Medical Parts
- Electronic Parts
- Tailored Machining
- Bicycle Parts
- Aluminum Machining
- Titanium Machining
- Stainless Steel Machining
- Copper Machining
- Brass Machining
- Super Alloy Machining
- Peek Machining
- UHMW Machining
- Unilate Machining
- PA6 Machining
- PPS Machining
- Teflon Machining
- Inconel Machining
- Tool Steel Machining
- More Material