The weight reduction ratio of aluminum alloy can reach about 125%
On July 12, the "2018 China Automotive Lightweight Industry Summit Forum" was grandly held in Shanghai. The theme of the forum was "new technologies, new materials, and new processes", aiming to reduce the weight of the car while increasing output power, reducing noise, and Maneuverability and safety, and discuss the development of automobile lightweight policy trends, vehicle lightweight platform design schemes, key component lightweight technology development, automotive lightweight multi-material application and cost control analysis.
1. The density of aluminum alloy is only about one-third of that of steel, but the thermal conductivity is three times higher than that of iron, and related studies have shown that the weight reduction ratio of aluminum alloy can reach about 125%, and the entire service life can be Reduce carbon dioxide emissions.
2. The products currently made by the Dongfeng Lightweight Research Center are mainly concentrated on the housing of the gearbox power system.
The content of my report is from three aspects. The first is the development trend of China's automotive lightweighting. The second is Dongfeng Motor's lightweight aluminum alloy application plan. My third low-pressure casting aluminum alloy lightweight application research case is simple. Share. I will not talk about the first part. I will mainly introduce Dongfeng's future lightweight planning. In the entire Dongfeng lightweight planning, Dongfeng will take advantage of the integration of parts and components to promote the development and application of lightweight technology. Mainly from three aspects, in the early stage of the development of Dongfeng limited lightweight, the goal is to establish CFT, integrate precision casting, cast aluminum and other parts business. The following table is the structure of the entire business. The lightweight technology is mainly concentrated in non-ferrous castings, PV and CV. Inside the two systems.
Where are aluminum alloys used in the overall lightweight? What are the benefits? The general knowledge of aluminum alloy and steel is well understood. Its density is only about one-third of that of steel, but its thermal conductivity is about three times higher than that of iron. Relevant studies have shown that the use of one kilogram of aluminum in a car can increase it by 2.25 For kilograms of steel, the weight reduction ratio of aluminum alloy can reach about 125%, and the entire life cycle can reduce carbon dioxide emissions, about 20 kilograms.
At present, the aluminum used in automobiles is roughly divided into cast aluminum and wrought aluminum alloy. We use gravity casting and pressure casting, and wrought aluminum alloy will account for 23% of the adoption rate. The scope of application will be used in some intake pipes, water pump housings, engine housings, etc. in the engine system. In the past, most of the gearbox shells were mostly cast bodies. These young quantitative needs, including some heavy-duty trucks, are also commonly used in aluminum alloys; the power system of passenger cars is mainly used in the gearbox housing, Retarder housing; bracket, swing arm, etc. for the post-processing of the chassis system.
The future lightweight research center Dongfeng is currently facing some products mainly concentrated on the top. The first row is the housing of the transmission power system. The first product is the front and rear housings of the Volvo 14-speed gearbox heavy truck gearbox. The second product is the front and rear shells of the 14-speed gearbox independently developed by Dongfeng. One of the two rear shells is the rear wheel hub of a certain Dongfeng model, plus the Dongfeng passenger car, Dongfeng Fengshen E70. The bracket mainly focuses on the combination of control ratio and steering, various brackets for the engine, and the chassis system includes the engine assembly and the bracket for the battery frame of the electric vehicle. Comparing the three major processes, the molding process of cast aluminum alloy generally uses high pressure, differential pressure, and low pressure gravity casting. At present, a large number of advertisements are also used. Extrusion molding is a process of aluminum alloy molding. Compared with the traditional three processes, low pressure casting has great advantages. The main reason is that compared with high pressure die casting, the mold cost including equipment investment cost is lower than that of high pressure die casting, and the mold life is worse than that of traditional high pressure die casting. And there is a very good advantage. If high-pressure die-casting is heat-treated, we will use some vacuum die-casting to effectively prevent gas from entering. Otherwise, if the gas cannot be quickly discharged during the molding process of traditional high-pressure die-casting, there will be difficulties in subsequent heat treatment. , Some vacuum high pressure die casting can also be used as a T6 process, but there is a corresponding cost to invest in it, and the cost of high pressure die casting will have a relatively large increase.
Next, I will share with you a few typical product cases that have been implemented in actual production. The first product is the two front and rear shells of the Dongfeng Volvo 14-speed gearbox. The weight of the entire front and rear shells is less than 30 kg. The material used is AlSi8Cu3. With traditional technology, we need to add a lot of process risers in the corresponding areas of these hot junctions. How to achieve it with low pressure technology? In the process of our research, these products have been manufactured without risers. All the risers have been made through the intervention of the outside of the mold to eliminate the risk of shrinkage and looseness of the hot junction, which effectively improves the overall product process yield rate. The production cycle of the entire product manufacturing has been shortened. Our production cycle is controlled between 5 and 6.5 minutes. This is the SOP product that was put into production in April 2016. These two pieces are mounted on Dongfeng Tianlong passenger cars and heavy trucks. On the model, Dongfeng is currently a star model.
The second gearbox, which is a traditional cast shell from the past. Through the optimization of the entire structure and the optimization of the system, it is converted from an iron shell to an aluminum shell. The structural characteristics of these two products are the same as those of Volvo. It is very similar, but we have made many structural optimizations suitable for aluminum alloy low-pressure casting in the process of converting from iron shell to aluminum shell, including the optimization of overall wall thickness and thermal junction. The materials used are similar. The weight reduction ratio of the conversion from iron shell to aluminum shell is up to 60%. Each product is different according to the structural characteristics of the product, and the weight reduction will be slightly different. Both products realize low-pressure manufacturing without risers. Craftsmanship, to achieve the quality goal, the production cycle is basically the same as the production cycle of the previous two products.
The following case is that our Dongfeng passenger car is also a new energy pure electric car from SOP last September. This product is mainly used on the E70 passenger car. This product is all stamped and welded parts, and bolts and nuts are connected. Through the optimization of the product and structure, our structure optimization not only meets the requirements of the entire function and load of the product, but also takes into account that we are suitable for the process structure. The weight of the optimized product is reduced from 25 kg to 14 kg, and the entire component is changed. It has 6 components. Among the 6 components are two small castings and 4 bolts. The structure is very simple and the transfer is very convenient. The actual weight reduction is up to 11 kg. Behind are some brackets on the engine. In the past, this kind of bracket used casting technology. After optimization, it was changed to low-pressure casting. The casting system of our later adopting low-pressure casting process is not of this structure, and has been well reduced. The characteristics of weight and cost reduction.
This is the bracket of the shift mechanism currently being made. This part is also stamped and welded and combined with bolts and nuts. The weight is 2.3 kg. The structure used is Q235 steel plate. The target for this part is 1.2 kg. After the optimization of the structure, an integral casting is realized. Basically, there is no change on the basis of the original wall thickness. The modal analysis of the structure after the optimization is not shown more, but the final result is shown to everyone. After optimization, the weight is about 1.0 kg, and the entire lightweight is reduced by 51%. The new energy water-cooled motor housing that is being developed later, the new energy is very hot now, the housing of the pure electric vehicle motor, this is relatively simple, the more complex motor housing has a lot of junction boxes and other connecting devices, this The feature of the product is a product with internal water channels. The thickness of the sand core is 6 mm and the net weight is 6.5 kg. The main feature of this product in the manufacturing process is that we adopt the automatic control of negative pressure exhaust technology during the manufacturing process. The gas produced by the middle sand core cannot be eliminated, and some concentrated large pores will be formed. What should I do with this gas? In addition to the control from the previous sand core process including the coating process, we need to add some forced exhaust space. We add some automatic exhaust devices. During the entire casting molding process, the sand is automatically exhausted by the wallpaper. The gas generated by the core can be effectively introduced to the outside to obtain a dense tissue.
The following are some products that we are developing next. The first two products are automatic gearboxes for heavy-duty trucks and 12-speed housings. This product is under development, samples have been released, and mass production molds are being designed. SOP will also be implemented in December 2019. The top product is also the rear housing of a 14-speed gearbox equipped with a hydraulic retarder on a Dongfeng heavy truck. In addition to the load requirement, this product has a complicated oil passage inside. The rear bracket is also a truck post-processing bracket, which is all aluminum alloy, which used to be cast steel.
Link to this article: The weight reduction ratio of aluminum alloy can reach about 125%
Reprint Statement: If there are no special instructions, all articles on this site are original. Please indicate the source for reprinting:https://www.cncmachiningptj.com
PTJ® provides a full range of Custom manufacturer of precision fabricated parts made from aluminum parts, brass parts, bronze, copper parts, high yield alloy, low carbon steel investment casting, high carbon steel and stainless steel alloy. Capable of handling parts up to +/-0.0002 in. tolerance. Processes include cnc turning, cnc milling, laser cutting,.ISO 9001:2015 &AS-9100 certified.
Tell us a little about your project’s budget and expected delivery time. We will strategize with you to provide the most cost-effective services to help you reach your target,You are welcome to contact us directly ( sales@pintejin.com ) .
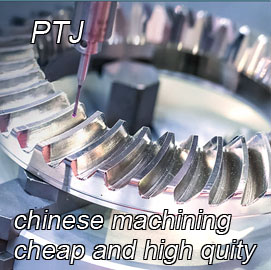
- 5 Axis Machining
- Cnc Milling
- Cnc Turning
- Machining Industries
- Machining Process
- Surface Treatment
- Metal Machining
- Plastic Machining
- Powder Metallurgy Mold
- Die Casting
- Parts Gallery
- Auto Metal Parts
- Machinery Parts
- LED Heatsink
- Building Parts
- Mobile Parts
- Medical Parts
- Electronic Parts
- Tailored Machining
- Bicycle Parts
- Aluminum Machining
- Titanium Machining
- Stainless Steel Machining
- Copper Machining
- Brass Machining
- Super Alloy Machining
- Peek Machining
- UHMW Machining
- Unilate Machining
- PA6 Machining
- PPS Machining
- Teflon Machining
- Inconel Machining
- Tool Steel Machining
- More Material