New breakthrough in 3D printing: tailor-made lenses with cornea
Patients with "deformed" cornea may wear custom 3D printed glasses in the future. Recently, I learned from Beijing Tongren Hospital that Dr. Song Hongxin, the deputy director of the Optometry Center of the hospital, is trying to use 3D printing technology to make custom lenses with "free-form surfaces". According to the individual corneal shape "tailor-made", showing an irregular mirror shape; 3D printing has been applied in many medical fields.
The surface of ordinary lenses is smooth and convex. "Free-form surface" means breaking through this regular smooth surface and presenting an irregular mirror shape. According to the shape of each person's cornea, it can accurately refract light and correct vision. The 3D printed lens can accurately fit the shape of the cornea and play a "tailor-made" effect.
This inspiration comes from NASA's adaptive optics system in the United States. The "blinking" of stars is a common optical phenomenon. Due to the constant changes of atmospheric turbulence, the light emitted by stars is affected when passing through the atmosphere and sometimes disappears, affecting astronomical observations. In order to smooth out the "noise", NASA uses an adaptive optics system for astronomical telescopes-a large deformable mirror composed of multiple small mirrors that can move freely. The deformable mirror will adjust the mirror surface after receiving the aberration signal sent by the system. , Correct aberrations, so that the stars do not "blink".
3D printed glasses are equivalent to a reduced "deformed mirror". The design drawing is derived from the shape of each patient's cornea. According to the "map", the printer prints out the lenses that fit the shape of the individual cornea layer by layer by spraying liquid. At present, Dr. Song Hongxin has initially realized the high-precision manufacturing of free-form surface lenses.
Traditional lenses are difficult to save irregular cornea
This special glasses is intended to solve the visual impairment of special populations-keratoconus is a primary corneal degeneration disease characterized by highly irregular myopic astigmatism and different visual impairments. The incidence of this disease in the population is 1 :2000, the disease generally starts in adolescence, and the cause of the onset is still unclear. The severe high-order aberrations caused by this disease will make ordinary glasses lose their effectiveness. Patients with corneal trauma, keratitis, and corneal transplantation may all develop high-order aberrations. This group has nearly one million people.
"The surface of the ordinary cornea is smooth and convex, but their cornea is pitted and pitted, and there are many irregular depressions." At the Tongren Hospital, Song Hongxin drew a corneal shape with severe high-order aberrations on paper-a curved curve, The central part presents wavy lines, like small smooth jagged teeth dug out on the side of the originally smooth hot spring egg.
In the case of normal vision, light from the outside passes through the cornea and is imaged on the human retina to form an accurate picture signal. Ordinary people with myopia need to adjust the imaging point by moving the imaging point back to keep the vision clear because the lens deforms and the light gathers in front of the retina. And once severe high-order aberrations appear, it means that when light passes through the potted cornea, it is refracted from various angles and forms a chaotic light track in the lens. Even if a pair of lenses is installed, it cannot be changed in the eyeball. The disorder. This is why ordinary glasses cannot save their eyesight.
If 3D printed free-form glasses become a reality, the lenses can be "coordinated" with the cornea, by adjusting different light refraction directions, so that they can be imaged in an orderly manner in the eye.
Song Hongxin said that traditional mirror-making technology may not be able to achieve this, but marketization has become unrealistic in the face of individualized needs. Each patient has a different cornea shape and a different curved surface of the lens, which means that each lens has to be made by a separate model and a separate assembly line, and the product will be sky-high. The advantage of 3D printing is that fine production can be achieved without additional cost.
3D printing has been involved in multiple medical fields
The advantages of 3D printing are considered to have broad prospects in the medical field. As early as 9 years ago, my country's medical institutions tried to get involved in this field.
In October 2009, two experts from the Department of Orthopedics of the Third Hospital of Beijing Medical University saw 3D printing equipment during their overseas academic exchanges, and realized that this kind of printing material may solve the problems that have always existed in artificial joints.
One of the orthopedic experts, Cai Hong, explained that the human bone structure naturally has many pores. If the metal surface can imitate its tiny and fully connected pores, human bones can grow into the pores, making the implant stronger. However, traditional artificial joints are produced by mold casting, and it is difficult to realize a layer of precise micro-pore coating on the metal surface. In contrast, 3D printing is computer modeling, manufactured by powder metallurgy, which can more flexibly design and produce artificial joints with precise pore structures.
From that year, the Third Hospital of Beijing Medical University began to conduct research on 3D printed implants for spinal surgery. In July 2015, my country's first 3D printed human implant developed by the institute was approved by the CFDA, which enabled 3D printed hip joints to enter the "mass production" era. In the following year, 3D printed vertebral body prostheses and intervertebral fusion cages were approved by CFDA, making my country an international leader in the field of 3D printed orthopedic surgery.
This is just one of the application cases of 3D printing in the medical field.
In September last year, the 3D printed dental implants, a key project led by Peking University Stomatological Hospital, completed animal experiments and entered clinical trials. Once the technology is widely used, the step of filling the gap between the bone and the implant with bone material will be omitted, reducing the difficulty of surgery and allowing more patients to benefit.
In foreign countries, researchers have developed a 3D printed heart stent that can self-adjust as children grow, avoiding the need for secondary surgery to replace implants during the growth process. The research on 3D printing of human organs such as artificial hearts has also attracted much attention.
Technical problems and achievement transformation problems to be solved
The prospects are bright and the road is bumpy. The clinical application of 3D printing still faces many technical difficulties. From hard bones to soft and complex human internal organs, people hope that 3D printing can bring more breakthroughs in treatment. However, the existing 3D printed hearts are expensive and can only beat for half an hour. 3D printed ligaments, tendons, and cartilage tissues Waiting is still at the stage of similarity, and functionality has not yet been realized.
In the field of optics, 3D printing is facing a virgin land.
“One of the core of 3D printing lies in materials. We are still looking for suitable optical materials.” Song Hongxin said that they have initially realized the high-precision manufacturing of free-form surface lenses, and the processing cost is reduced by more than 10 times compared with traditional methods. However, due to lack of experience, the difficulty of the material still needs to be broken through. The photosensitive material they are currently using will deform during curing, which will affect the refraction effect.
In addition, he looks forward to getting more support in legal, market and other professional fields in the process of transforming the results.
The reporter learned that in recent years, the transformation of scientific and technological achievements has received increasing attention. In April 2016, the State Council issued the "Action Plan for Promoting the Transfer and Transformation of Scientific and Technological Achievements"; in September of the same year, the former National Health and Family Planning Commission published the "Guiding Opinions on Strengthening the Transfer and Transformation of Health and Health Scientific and Technological Achievements", proposing the transfer and transformation of scientific and technological achievements It is an important content of health and health science and technology innovation, and is of great significance to promoting the construction of a "healthy China".
Song Hongxin hopes that in the future, my country will also be able to establish a related achievement transformation mechanism to allow professionals from finance and law to join, so as to improve the transformation efficiency of medical innovation achievements and reduce the risk of industrialization.
Link to this article: New breakthrough in 3D printing: tailor-made lenses with cornea
Reprint Statement: If there are no special instructions, all articles on this site are original. Please indicate the source for reprinting:https://www.cncmachiningptj.com
PTJ® provides a full range of Custom manufacturer of precision fabricated parts made from aluminum parts, brass parts, bronze, copper parts, high yield alloy, low carbon steel investment casting, high carbon steel and stainless steel alloy. Capable of handling parts up to +/-0.0002 in. tolerance. Processes include cnc turning, cnc milling, laser cutting,.ISO 9001:2015 &AS-9100 certified.
Tell us a little about your project’s budget and expected delivery time. We will strategize with you to provide the most cost-effective services to help you reach your target,You are welcome to contact us directly ( sales@pintejin.com ) .
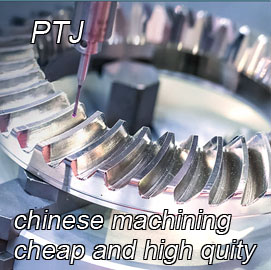
- 5 Axis Machining
- Cnc Milling
- Cnc Turning
- Machining Industries
- Machining Process
- Surface Treatment
- Metal Machining
- Plastic Machining
- Powder Metallurgy Mold
- Die Casting
- Parts Gallery
- Auto Metal Parts
- Machinery Parts
- LED Heatsink
- Building Parts
- Mobile Parts
- Medical Parts
- Electronic Parts
- Tailored Machining
- Bicycle Parts
- Aluminum Machining
- Titanium Machining
- Stainless Steel Machining
- Copper Machining
- Brass Machining
- Super Alloy Machining
- Peek Machining
- UHMW Machining
- Unilate Machining
- PA6 Machining
- PPS Machining
- Teflon Machining
- Inconel Machining
- Tool Steel Machining
- More Material