Development of fast fuse manufacturing 3D printer, printing speed increased by 10 times
On December 10, it was reported that Professors Jamison Go and John Hart of the Massachusetts Institute of Technology (MIT) have developed a new 3D printer. It is 10 times that of the current FDM 3D printer.
Desktop 3D printers are great for creating high-quality and complex parts on demand, but their biggest weakness is always slow. They can only print one object at a time and only one thin layer at a time. There are four main factors that limit the speed of FDM / FFF 3D printers: the force applied to the wire when the wire is pushed into the nozzle; how fast the heat is transferred to the wire; the speed at which the print head moves around the build area; and the material The rate of curing after extrusion because it needs to support the next layer.
They, like most other developers, solve the curing problem by blowing air on the printed model. The remaining obstacles require more creativity. When pushing the wire, it is usually done by running between the driving gear and the idler; tension is applied to the driving gear, and when the driving gear rotates, the gear bites into the wire and pushes it down. If the tension on the wire is too large, the drive gear will enter the wire and eventually lose its grip before the plastic accumulates, while too little tension will cause slippage and gaps during extrusion.
Go and Hart decided to pass the wire through a threaded nut and use the threaded nut to drive the consumable; when the nut is rotated by the motor (via a belt), the wire drops. When the nut rotates, the anti-twist roller can prevent the filament from twisting. This extrusion method is not only faster than a typical drive gear unit, but also more precise.
The laser solves the problem of the speed of heating the wire, which is enough to completely melt the wire. The quartz cavity is lined with a reflector. When the wire passes through the chamber, the laser bounces inside and preheats the wire before the wire passes through the traditional heating block.
Finally, Go and Hart designed a servo-driven parallel gantry system that can move the print head quickly and accurately with almost no gaps. Most desktop 3D printers will jitter or fluctuate when the printing speed is too fast. Here, speed is mainly achieved through the use of heavy-duty frames and powerful motors rather than novel solutions.
The new printer attracted competitors in the speed test, including a commercial 3D printer worth $100,000. The 3D printer manufactured by the research team is priced at $15,000, so it is unlikely to be available soon. This extrusion method is 7 to 10 times faster and can produce 127 cubic centimeters per hour. The print quality may be better and may be improved by adjusting the retraction and path settings, but considering the speed of 3D printing, the quality is still very good.
Hart also collaborated with Sebastian Pattinson, a lecturer at the University of Cambridge, to demonstrate a 3D printing technique using cellulose. Cellulose is cheap, renewable, and has ideal mechanical properties, but because cellulose is easily decomposed when heated, 3D printing with cellulose has proven difficult. By treating the cellulose with acetate, they can dissolve it in acetone and successfully extrude it with a 3D printer. The acetone evaporates (and is captured), leaving only the cellulose acetate. Finally, the acetate is removed with a sodium hydroxide bath, and the result is the cellulose part. The two 3D printed a set of medical tweezers, and even injected an antibacterial dye into the 3D printed parts, which increased the resistance to bacteria by 95%.
Link to this article: Development of fast fuse manufacturing 3D printer, printing speed increased by 10 times
Reprint Statement: If there are no special instructions, all articles on this site are original. Please indicate the source for reprinting:https://www.cncmachiningptj.com
PTJ® provides a full range of Custom manufacturer of precision fabricated parts made from aluminum parts, brass parts, bronze, copper parts, high yield alloy, low carbon steel investment casting, high carbon steel and stainless steel alloy. Capable of handling parts up to +/-0.0002 in. tolerance. Processes include cnc turning, cnc milling, laser cutting,.ISO 9001:2015 &AS-9100 certified.
Tell us a little about your project’s budget and expected delivery time. We will strategize with you to provide the most cost-effective services to help you reach your target,You are welcome to contact us directly ( sales@pintejin.com ) .
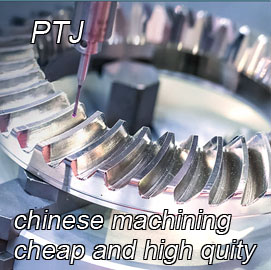
- 5 Axis Machining
- Cnc Milling
- Cnc Turning
- Machining Industries
- Machining Process
- Surface Treatment
- Metal Machining
- Plastic Machining
- Powder Metallurgy Mold
- Die Casting
- Parts Gallery
- Auto Metal Parts
- Machinery Parts
- LED Heatsink
- Building Parts
- Mobile Parts
- Medical Parts
- Electronic Parts
- Tailored Machining
- Bicycle Parts
- Aluminum Machining
- Titanium Machining
- Stainless Steel Machining
- Copper Machining
- Brass Machining
- Super Alloy Machining
- Peek Machining
- UHMW Machining
- Unilate Machining
- PA6 Machining
- PPS Machining
- Teflon Machining
- Inconel Machining
- Tool Steel Machining
- More Material