Method for predicting the formation of metal 3D printing defects
In the 3D printing process, if gas is trapped in the metal powder supplied to the 3D printer, tiny air pockets may appear. These areas have a Swiss cheese-like structure, are less dense and weaker than the surrounding environment, which can cause cracks and other failures.
Research teams from Carnegie Mellon University and the U.S. Department of Energy (DOE) Argonne National Laboratory have identified these cavitations and created a method to predict the formation of cavitations. This information can significantly improve the 3D printing process, and their research was published last week in the journal Science.
"The research in this article will translate into better quality and better machine control," said Anthony Rollett, professor of materials science and engineering at Carnegie Mellon University and the author of the paper. "For most companies, for additive manufacturing to really take off, we need to improve the consistency of the finished product. This research is an important step in this direction."
Scientists used extremely bright high-energy X-rays on the Advanced Photon Source (APS) of Argonne, the Office of Scientific User Facilities of the U.S. Department of Energy, to take ultra-high-speed video and images of the laser fusion (LPBF) process, where the laser was used to powder the material Melt and fuse together.
The laser scans each layer of powder to melt the metal, literally creating a finished product from scratch. When tiny air pockets are trapped in these layers, defects can form. These defects can cause blemishes, leading to cracks or other failures in the final product.
So far, manufacturers don’t know much about how lasers create pores in metal. However, they believe that the fault lies in the type of metal powder or the intensity of the laser. Therefore, manufacturers have been using different types of metals and laser trial and error methods to seek to reduce defects.
In fact, studies have shown that these vapor depressions exist in almost all conditions of the process, whether it is laser or metal.
Rollett said: "We are lifting the veil and revealing the real situation. Most people think that you shine a laser on the surface of metal powder. The light is absorbed by the material and the metal is melted into a molten pool. In fact, you really drill a hole in the metal Hole."
Using one of the most powerful synchronous accelerator devices in the world, the researchers observed that the researchers observed what happens when the laser passes through a bed of metal powder.
Under perfect conditions, the shape of the molten pool is shallow and semicircular, which is called "conduction mode". But in the actual printing process, a high-power laser that usually moves at a low speed can change the shape of the molten pool to a certain shape. Like a keyhole in a keyhole: round and large at the top, with a narrow spike at the bottom. This "keyhole mode" melting can potentially lead to defects in the final product.
This image was taken under the synchrotron of the Argonne National Laboratory and shows the keyhole gap that will be formed during the metal 3D printing process. During the laser powder bed fusion, the 3D printer "drilled" a hole in the metal.
"Based on this research, we now know that the keyhole phenomenon is more important in many ways than the powder used in additive manufacturing," said Ross Cunningham, who recently graduated from Carnegie Mellon University and is one of the co-first authors. . "Our research shows that you can predict the factors that cause the keyhole-which means you can also isolate these factors for better results."
Studies have shown that when a certain laser power density is reached that is sufficient to make the metal boil, keyholes are formed. In turn, this reflects the importance of laser focus in the additive manufacturing process, a factor that has received little attention so far, the research team said.
"Due to the expertise developed by Argonne, the keyhole phenomenon can be seen for the first time in this detail," said Tao Sun, an Argonne physicist and paper author. "Of course, the strong high-energy X-ray beam of APS is the key."
The research team believes that this research can inspire manufacturers of additive manufacturing machines to provide greater flexibility in controlling the machines, and that improved use of the machines can lead to significant improvements in the final product.
"This is important because 3D printing is generally quite slow," Rollett said. "It takes hours to print a part that is a few inches tall. If you can afford the technology, that's okay, but we need to do better."
Link to this article: Method for predicting the formation of metal 3D printing defects
Reprint Statement: If there are no special instructions, all articles on this site are original. Please indicate the source for reprinting:https://www.cncmachiningptj.com
PTJ® provides a full range of Custom manufacturer of precision fabricated parts made from aluminum parts, brass parts, bronze, copper parts, high yield alloy, low carbon steel investment casting, high carbon steel and stainless steel alloy. Capable of handling parts up to +/-0.0002 in. tolerance. Processes include cnc turning, cnc milling, laser cutting,.ISO 9001:2015 &AS-9100 certified.
Tell us a little about your project’s budget and expected delivery time. We will strategize with you to provide the most cost-effective services to help you reach your target,You are welcome to contact us directly ( sales@pintejin.com ) .
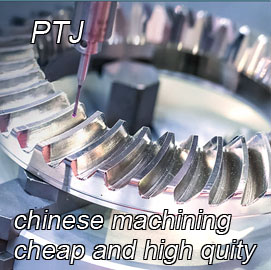
- 5 Axis Machining
- Cnc Milling
- Cnc Turning
- Machining Industries
- Machining Process
- Surface Treatment
- Metal Machining
- Plastic Machining
- Powder Metallurgy Mold
- Die Casting
- Parts Gallery
- Auto Metal Parts
- Machinery Parts
- LED Heatsink
- Building Parts
- Mobile Parts
- Medical Parts
- Electronic Parts
- Tailored Machining
- Bicycle Parts
- Aluminum Machining
- Titanium Machining
- Stainless Steel Machining
- Copper Machining
- Brass Machining
- Super Alloy Machining
- Peek Machining
- UHMW Machining
- Unilate Machining
- PA6 Machining
- PPS Machining
- Teflon Machining
- Inconel Machining
- Tool Steel Machining
- More Material