Solve the three major pain points of die casting enterprises
In recent years, the country has paid more and more attention to environmental protection, and environmental protection laws and regulations have become increasingly stringent. The reduction of consumption and cost for die-casting enterprises has become an urgent problem to be solved, and the recycling and reuse of release agent is one of many problems. Combining years of experience in R&D, production and use of release agents, and the Suzhou Research Institute of Shandong University, through continuous technical improvement and practical operation, successfully developed a release agent recycling energy-saving system with independent intellectual property rights.
In terms of cost, the release agent re-recycling system introduces Internet of Things technology to realize the monitoring and adjustment of all parameters of recovery, liquid distribution, air pressure, pump pressure, liquid supply, concentration, and control personnel operation, and cloud big data analysis is scientific Management provides a basis for decision-making and effectively controls production costs; real-time detection of the amount of waste liquid recovered, intelligent adjustment of the amount of release agent used, to prevent waste liquid.
In terms of management, the new equipment system runs fully automatically and uses big data records to facilitate storage and technical staff to call and view. It can be combined with the big data billboards of advanced enterprises to carry out digital management and control of the unit cost of die castings.
In terms of environmental protection, the use of multi-machine separation technology, advanced ozone sterilization technology, and advanced online concentration real-time detection technology have laid a more feasible technical foundation for the recycling of release agents.
Release agent recycling system
The successful research and development of this high-end environmentally friendly intelligent release agent regeneration system breaks the conventional structure and introduces the design of the filling body structure to reduce the probability of scaling. The multi-stage dimensional inclined tube pretreatment pool design effectively improves the efficiency of slag removal and oil filtration. It is not easy to breed bacteria and realizes automatic sterilization and slag removal. In addition, the use of the SM effect can effectively inhibit the agglomeration of bacteria and effective substances in the release agent, and improve the quality of the release agent; even in extreme conditions, the four-fold backup ratio system can ensure the normal and stable operation of the equipment, even if it is repaired normally. It will not affect the normal production cycle.
In addition, all tanks of the system have automatic sterilization and cleaning functions, and support one-key cleaning of a single tank.
Mr. Fang Zhijie said that the release agent purified by the energy-saving system can be automatically proportioned and fully automated and uninterrupted to achieve 100% recovery of the waste liquid. The sterilization rate is 99%. The release agent is waste. The liquid recovery rate can reach 30% of the total cost. At the moment when the die casting industry is facing many unfavorable factors, it can help companies save a lot of redundant costs.
"In the sewage treatment of die-casting enterprises, the sewage containing the release agent waste liquid is calculated at 300 yuan/ton, and the monthly release agent is 10T, and the sewage needs to be treated in a year of 800T/month*12 months. This is not a small amount. Wastewater treatment and labor costs.” Mr. Fang Zhijie calculated the economic account to the reporter on the spot, “If you rely on the release agent to recycle the energy-saving system, you can save 30% of the cost of the release agent. The cost can be recovered in less than a year, which can reduce a lot of burdens on die-casting companies."
"Before using this set of equipment, our company also helped customers to perform laboratory analysis of the recovered liquid, compare the missing components of the waste liquid, and then scientifically and rationally add the appropriate stock solution, which effectively guarantees the quality of the release agent product." Mr. Fang Zhijie explained to customers very rigorously.
Link to this article: Solve the three major pain points of die casting enterprises
Reprint Statement: If there are no special instructions, all articles on this site are original. Please indicate the source for reprinting:https://www.cncmachiningptj.com
PTJ® provides a full range of Custom manufacturer of precision fabricated parts made from aluminum parts, brass parts, bronze, copper parts, high yield alloy, low carbon steel investment casting, high carbon steel and stainless steel alloy. Capable of handling parts up to +/-0.0002 in. tolerance. Processes include cnc turning, cnc milling, laser cutting,.ISO 9001:2015 &AS-9100 certified.
Tell us a little about your project’s budget and expected delivery time. We will strategize with you to provide the most cost-effective services to help you reach your target,You are welcome to contact us directly ( sales@pintejin.com ) .
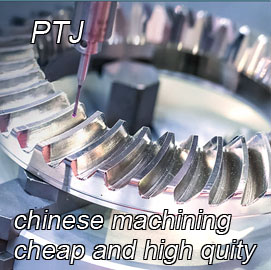
- 5 Axis Machining
- Cnc Milling
- Cnc Turning
- Machining Industries
- Machining Process
- Surface Treatment
- Metal Machining
- Plastic Machining
- Powder Metallurgy Mold
- Die Casting
- Parts Gallery
- Auto Metal Parts
- Machinery Parts
- LED Heatsink
- Building Parts
- Mobile Parts
- Medical Parts
- Electronic Parts
- Tailored Machining
- Bicycle Parts
- Aluminum Machining
- Titanium Machining
- Stainless Steel Machining
- Copper Machining
- Brass Machining
- Super Alloy Machining
- Peek Machining
- UHMW Machining
- Unilate Machining
- PA6 Machining
- PPS Machining
- Teflon Machining
- Inconel Machining
- Tool Steel Machining
- More Material