Develop new DDM "indirect metal 3D printing" technology
On April 10th, the Changsha Mercury team explored a new type of "indirect metal 3D printing" technology. They developed a special "metal paste" that can be completed by using a very cheap ceramic clay 3D printer. 3D printing of parts. Since the printing process does not require heating, this mode can be called DDM (Direct Deposition Modeling) technology.
From automotive metal parts to aircraft engines and other aerospace components, metal 3D printing brings endless imagination to people and represents the true development direction of intelligent manufacturing in the future.
The current rapid prototyping methods that can be used to directly manufacture metal functional parts include: Selective Laser Sintering (SLS) technology, Direct Metal Laser Sintering (DMLS), Selective Laser Melting, SLM technology, Laser Engineered Net Shaping (LENS) technology and Electron Beam Selective Melting (EBSM) technology, etc. The industry refers to these technologies as "direct metal 3D printing technologies." These technologies all involve expensive high-energy equipment such as lasers or electron beams, and their use and maintenance costs are relatively high; in addition, the low printing efficiency is often criticized by those in the industry.
At present, there is a wave of research and development of "indirect metal 3D printing technology" around the world. Use mature metal injection molding (MIM), adhesive injection, FDM melt extrusion technology and a combination of these technologies to complete the final molding of metal parts. Compared with laser or electron beam equipment, the equipment used in "indirect metal 3D printing technology" is much "cheap", and the printing speed can be increased by more than a hundred times, showing a certain competitive advantage. Some companies with core technology of indirect printing have received extensive attention from the capital market, and the scenery is boundless; for example, companies such as Markforged and Desktop Metal have received large financing of more than 1 billion US dollars.
Calm down and analyze, everyone found that most of the so-called "indirect metal 3D printing technologies" are some kind of "deformed" FDM+MIM technology combination. The materials used can be in the form of filaments or granules, and are composed of metal powder coated with plastic polymers. First, use FDM technology to heat, melt, extrude, and cool these filamentary or granular materials to form a "green embryo"; then use special equipment to remove the plastic polymer in the "green embryo"; and finally perform high temperature Sintering to form the final metal part. Since the "green embryo" contains a higher proportion of plastic polymers, subsequent high-temperature sintering will produce a larger proportion of shrinkage (more than 17%); in addition, there is a more difficult problem of asymmetric shrinkage. The binder jet technology also has the above-mentioned problems, and the sintered density of metal parts is also less than the FDM+MIM technology combination scheme, which is now at the edge of technology.
In the field of ceramic clay 3D printing, based on the FDM model, relatively sophisticated ceramic clay 3D printing equipment has been developed in recent years; ordinary ceramic clay (porcelain clay) can be directly printed and formed. Since heating is not required, this mode can be called DDM (Direct Deposition Modeling) or NTDM (Normal Temperature Deposition Modeling) technology.
The Changsha Mercury team took a different approach and developed a special "metal clay", pioneering a new DDM technology in the field of "indirect metal 3D printing". "Metal clay" is made by mixing metal powder with special composition and special polymer binder. Its appearance is similar to ordinary clay, and it can be shaped and carved. The Mercurial team used ordinary cheap clay 3D printers to print this "metal clay" into a "green embryo" without heating.
The printing accuracy of this new "metal clay" material (gray) exceeds that of ordinary clay (porcelain clay) (white). The "green embryo" does not need to be degummed, and can be directly put into a special vacuum furnace for sintering, and finally becomes a dense metal product with few voids.
In addition to high strength, metal products produced in DDM mode can also have super corrosion resistance (up to 2-5 times that of stainless steel); by adjusting the formula, super wear-resistant parts with complex shapes can be produced (for example, it can be produced Cermet wear-resistant parts with hardness around HRC62). These high value-added properties are beyond the reach of the existing "indirect metal 3D printing technology", and they are highly competitive.
In Antarctic Bear’s view, the core of this new technology lies in the configuration of the metal slurry. In terms of equipment, very cheap ceramic clay 3D printers can be used to complete the molding, which greatly reduces the manufacturing cost. However, the Changsha Mercury team still has a lot of work to do in terms of dimensional accuracy of metal parts, sintering shrinkage, and composition of metal parts.
The Changsha Mercury team was founded in January 2019. The team is committed to the research and development of new 3D printing materials, equipment and processes. Li Xin is the team leader and graduated from the Institute of Metal Research, Chinese Academy of Sciences. Gu Li Xin introduced that the new type of "metal clay" developed by the team can solve the problems of sintering shrinkage and asymmetric deformation; this new type of DDM technology mode can develop completely new "indirect functions" beyond the laser (electron beam) printing path. Sex metal 3D printing technology", everyone will wait and see!
Link to this article: Develop new DDM "indirect metal 3D printing" technology
Reprint Statement: If there are no special instructions, all articles on this site are original. Please indicate the source for reprinting:https://www.cncmachiningptj.com
PTJ® provides a full range of Custom manufacturer of precision fabricated parts made from aluminum parts, brass parts, bronze, copper parts, high yield alloy, low carbon steel investment casting, high carbon steel and stainless steel alloy. Capable of handling parts up to +/-0.0002 in. tolerance. Processes include cnc turning, cnc milling, laser cutting,.ISO 9001:2015 &AS-9100 certified.
Tell us a little about your project’s budget and expected delivery time. We will strategize with you to provide the most cost-effective services to help you reach your target,You are welcome to contact us directly ( sales@pintejin.com ) .
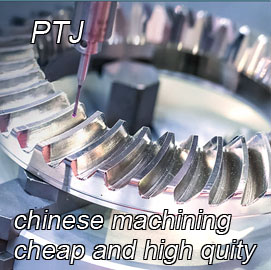
- 5 Axis Machining
- Cnc Milling
- Cnc Turning
- Machining Industries
- Machining Process
- Surface Treatment
- Metal Machining
- Plastic Machining
- Powder Metallurgy Mold
- Die Casting
- Parts Gallery
- Auto Metal Parts
- Machinery Parts
- LED Heatsink
- Building Parts
- Mobile Parts
- Medical Parts
- Electronic Parts
- Tailored Machining
- Bicycle Parts
- Aluminum Machining
- Titanium Machining
- Stainless Steel Machining
- Copper Machining
- Brass Machining
- Super Alloy Machining
- Peek Machining
- UHMW Machining
- Unilate Machining
- PA6 Machining
- PPS Machining
- Teflon Machining
- Inconel Machining
- Tool Steel Machining
- More Material